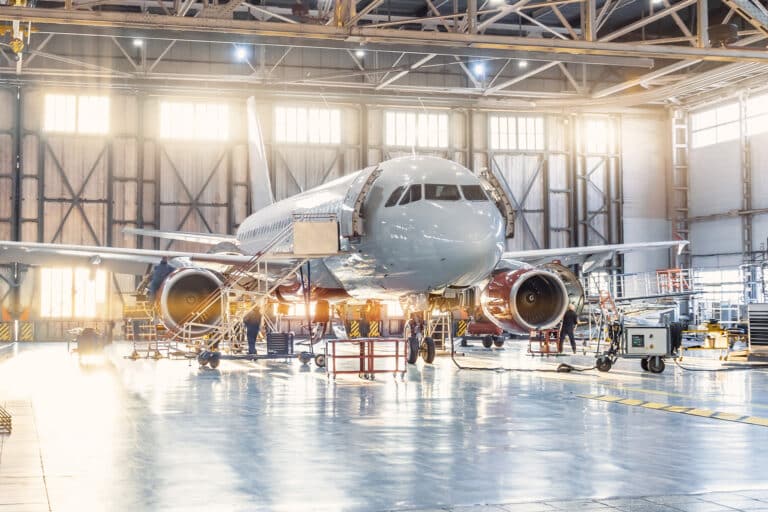
Going beyond lean manufacturing
The UK’s aerospace industry has seen significant improvements in productivity but the truth is that much more could be achieved by accelerating the adoption of digital technologies and enriching the skills base.
Global instability is driving increases in defence spending and more international co-operation with programs like AUKUS and GCAP driving leading players to consider how they make a generational shift in manufacturing capability. In the civil aerospace sector, with passenger numbers predicted to rise to a record level in 2024, and demand for new aircraft increasing, OEMs and their suppliers also know that they need to stay focused on driving efficiency and boosting productivity. Could this be the year that they put their ‘factory of the future’ strategies to the test?
According to International Air Transport Association (IATA), an estimated 4.7 billion people are expected to take flights in 2024: more than the 4.5 billion passengers recorded in 2019. While this is good news for the sector as a whole, it means that rate ramp up pressures, which have been affecting many OEMs and their suppliers since the pandemic, are not over yet.
While lean principles and automated systems have been widely used by many primes, OEMs and Tier 1 suppliers for decades, not all have achieved the same level of sophistication, and many have yet to realise the full potential of data and advanced digital technologies, enabled by AI and the Internet of Things (IoT). With the rate ramp up ongoing, businesses will need to speed up their change programmes and implement their factory of the future visions to stay competitive.
In an industry where quality, regulation and reliability are critical, you may wonder why some aerospace and defence manufacturers have been slow to embrace digitalisation. However, there is now a palpable sense of urgency in the sector, and OEMs are keen to press ahead with the development and implementation of factory of the future strategies; pushing for efficiency-driving changes across the value chain.
The factory of the future is not a new concept, but few Boards have a complete understanding of what it could look like for their business. It should be considered as the next evolution in a company’s digital transformation; a chance for manufacturers to harness cutting edge Internet of Things (IoT) and other technologies to enhance connectivity and data visibility across their organisations and their supply chains too.
Once fully enabled, the factory of the future will bring many efficiency benefits by streamlining flows from Manufacturing Execution System (MES) and advanced Material Requirements Planning (MRP), right through to operations on the shop floor and increasing real-time data visibility, allowing decision makers to make better-informed decisions more quickly, and unlocking flexibility. Data-based models can be developed to help the business to predict and smooth out demand fluctuations, supply chain disturbances or other variables. They can also be used to predict Maintenance Repair and Operations (MRO) demand and mitigate the risk of equipment downtime.
Most factory of the future strategies make use of digital twinning. Using advanced simulation technologies, digital representations of assets, such as machinery, people, or processes are produced to test the end-to-end impact of specific changes or modifications. Digital twins can help decision makers to make better decisions more quickly based on the exact status of the factory – its people, processes and machinery – at any one time. They can also help to direct capital investment. For example, in the factory of the future, automated systems could be applied more strategically to areas where they bring most value.
Improving process efficiency will help to improve profitability of course, but it can also support manufacturers on their sustainability journeys. With access to real-time data about production processes, manufacturers might take decisions to regulate inputs and outputs in a way that facilitates lower energy consumption, for example. Improved connectivity across the value chain also means there could be opportunities for OEMs and Tier 1 and 2 suppliers to collaborate to innovate sustainable solutions or switch to low-carbon components or materials.
Digitalisation is transforming the aerospace and defence industries at pace and manufacturers can’t afford to get left behind. With the help of a factory of the future vision and harnessing operational and process data, there is an opportunity for manufacturers to outperform the competition in both profitability and sustainability.
Sign up to get the latest insights from Vendigital
Improve your operational performance
Related Insights
The UK’s aerospace industry has seen significant improvements in productivity but the truth is that much more could be achieved by accelerating the adoption of digital technologies and enriching the skills base.
Manufacturers need to collaborate closely with suppliers to mitigate the impact of shocks and supply chain disruptions.
The boom in Generative AI is creating new opportunities for aerospace and defence sector manufacturers. Used correctly, GenAI capability can help to optimise production processes, improve supply chain resilience, ringfence knowledge and reduce costs.
Subscribe to our newsletter