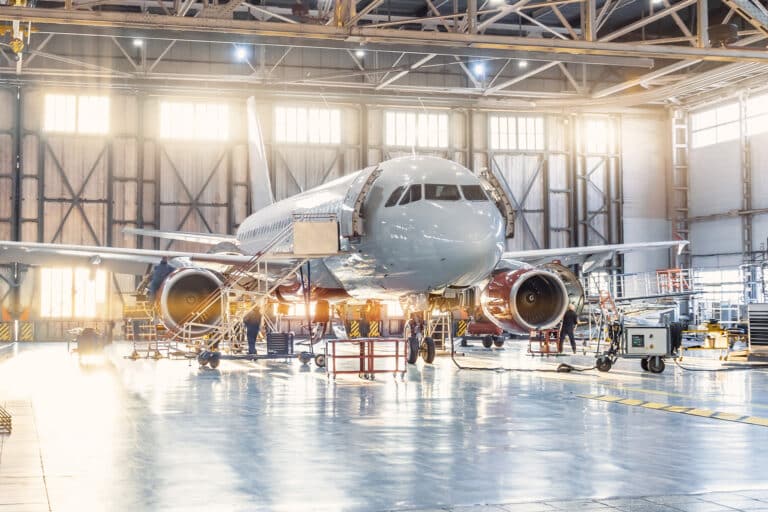
Going beyond lean manufacturing
The UK’s aerospace industry has seen significant improvements in productivity but the truth is that much more could be achieved by accelerating the adoption of digital technologies and enriching the skills base.
The past few years have seen significant increases in demand for new aircraft, and there are no signs this will stop anytime soon. Despite work to ramp-up production, there is still a gap in the market as supply chains struggle to keep up with this demand.
An ADS report published at the end of last year showed a 354% year on year increase in November aircraft orders, which pushed the backlog to a record high for the 4th year running. At the time, the backlog stood at 14,839 aircrafts – a 10% increase on the previous year.
With more work needed to meet growing demand for aircraft parts and raw materials, businesses at all levels of the supply chain must ensure they are operating as efficiently as possible, so they can bring on the capacity needed, while taking steps to mitigate risks.
Data is key to developing a robust understanding of the risks and opportunities that exist in a buoyant market. As well as analysing shifting customer data, businesses should draw on diverse open source and cross supply chain data to gain an accurate view of where demand is coming from, when and how much. When overlaid with qualitative data gleaned from in-person site visits, this combined supply chain and market overview allows businesses to identify pressure points and areas of opportunity that might otherwise fall under the radar.
When assessing the risks and opportunities that might exist within a specific supply chain, it can be helpful to group suppliers according to commodity. Where there are issues with the supply of a specific commodity for example, businesses may wish to introduce other areas of data, for example by drawing on information from industry bodies. Score cards can also be developed to provide operations and procurement teams with a reliable picture of the risks and opportunities inherent in each supply chain, validated against supplier performance. As well as ‘scoring’ suppliers in terms of their capacity and risk exposure, it is important to consider how well they might have performed in rate ramp up situations previously.
When conducting a rate readiness assessment of any supply chain, the process should be iterative. This is because most industries tend to use the same suppliers for certain core components or raw materials, so risks affecting their supply may only come to light after visiting a business further up the chain. If a weak point in the value chain is identified, it may be necessary for OEMs to shift their source of supply to mitigate the risk of disruption or establish a dual-sourcing arrangement. For good reason, moving products around the supply chain is often seen as costly and time consuming. However many ramp-up issues can be spotted based on previous performance. Therefore, once a process and toolset is in place, reviews of this nature should ideally be used to monitor supply chain performance on an ongoing basis, so early action can be taken.
The aerospace and defence sector has not been immune to the well-documented issues surrounding labour and skills shortages and this has undoubtedly brought challenges for many organisations in recent months. However there are systemic, underlying factors that must be addressed if the industry is to truly learn lessons from previous rate increases.
The most common of these is load and capacity planning. For what is largely a process driven industry, there exists huge variation in the way in which load and capacity planning is carried out. In both large and small organisations, greater focus in this area represents a significant opportunity to drive performance. Although businesses continue to spend millions implementing new ERP systems in the hope that they will solve problems in this area, many would achieve the same or better results through rigorous and consistent process application or better use of data and analytics to understand and refine existing planning systems. There are also opportunities to improve collaboration between businesses, including the open sharing of data to enable lines of supply to be optimised.
When aiming to drive efficiency in any organisation, data is key. Rather than treating each rate assessment as a one-off activity, businesses should make it part of their business as usual. Indeed keeping data under review will ensure they are ready to meet future market demand and periodically running sessions with supply chain teams to learn lessons during ramp up should make it possible to address future issues before they arise.
It is also essential that business realise the stress and pressure that increasing rates put on people, particularly in operational and supply chain roles. Businesses need to be aware of this and take action to relieve pressure on individual employees or boost resources where needed. This should include finding ways to allow teams to run planning processes that can ultimately support recovery.
Wherever they sit in the supply chain, from OEM to raw material supplier, being prepared to meet demand-side challenges could be critical to a business’ long-term survival, but equally it could create valuable opportunities to strengthen market share.
Take control of your costs – book a 30 minute slot with one of our cost transformation experts
Curious how you could accelerate the journey to cost reduction in your business? Book a free, no-obligation 30-minute consultation with one of our cost transformation experts to discuss your current operational challenges, specific ambitions and explore tailored strategies to achieve your cost reduction goals.
To benefit from our team’s deep operational expertise, simply click the link below and we’ll come right back to you.
Sign up to get the latest insights from Vendigital
Related Insights
The UK’s aerospace industry has seen significant improvements in productivity but the truth is that much more could be achieved by accelerating the adoption of digital technologies and enriching the skills base.
Manufacturers need to collaborate closely with suppliers to mitigate the impact of shocks and supply chain disruptions.
The boom in Generative AI is creating new opportunities for aerospace and defence sector manufacturers. Used correctly, GenAI capability can help to optimise production processes, improve supply chain resilience, ringfence knowledge and reduce costs.
Subscribe to our newsletter
Take control of your costs – book a 30 minute slot with one of our cost transformation experts
Book a free, no-obligation 30-minute consultation with one of our cost transformation experts to discuss your current operational challenges, specific ambitions and explore tailored strategies to achieve your cost reduction goals.