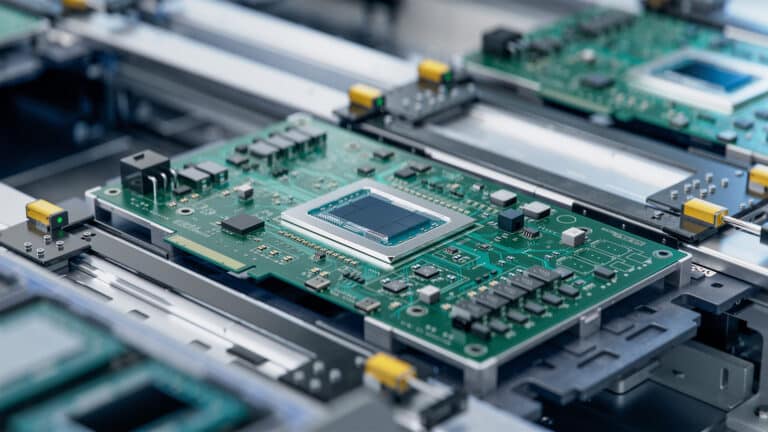
Can Britain compete in global semiconductor manufacturing?
The importance of semiconductor manufacturing across the globe can’t be overestimated. The question is, can the UK capitalise on its position of strength to become a global leader in semiconductor manufacturing?