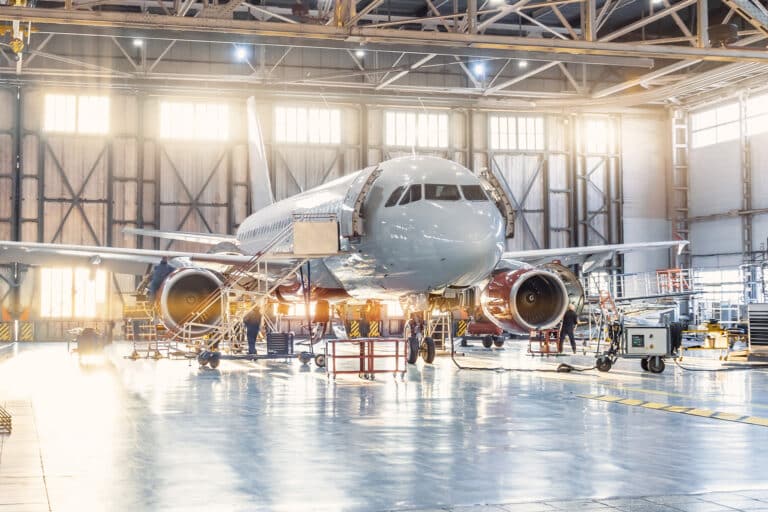
Going beyond lean manufacturing
The UK’s aerospace industry has seen significant improvements in productivity but the truth is that much more could be achieved by accelerating the adoption of digital technologies and enriching the skills base.
Introduction
Ramping up is challenging at the best of times, but become even more complicated when it needs to be balanced against other demands. For aerospace manufacturers a rapid increase in orders over the last few years has coincided with pressure to increase resilience, sustainability and keep up with technological advances that are changing the landscape of the industry.
This report sheds light on the challenges that many aerospace and defence sector businesses are facing, and will continue to face, as production rates increase. Key to their success is balancing the need to improve their own operational performance while optimising supply chain efficiency.
By sharing the experiences of a major Aerospace & Defence (A&D) sector manufacturer and setting out some strategies for success, this report aims to share best practice across industry sectors. These strategies are designed to help high-value manufacturers to improve supply chain resilience and survive and thrive in a growing market.
With rate increases in the A&D industry already underway, those that focus on collaboration and ensure that their preparations stay ahead of the demand curve will be best placed to make the most of the ongoing ramp-up opportunity.
Did you know
November marked the fourth consecutive record-breaking backlog of aircraft orders, which now totals almost 15,000.
Source: ADS 2023
Airbus has forecast that there will be demand for 39,490 new commercial aircraft between 2022-2041, of which 31,620 will be single aisle aircraft.
Source: Airbus Global Market forecast 2022-2041
“Ramping up is always a time of heightened risk for any manufacturer, not least those with complex, global supply chains. For those that succeed, however, there are potential rewards – opportunities to strengthen customer relationships, differentiate products and services, and increase market share.”
Paul Adams, Director, Vendigital
1
The ramp-up challenge
When airline passenger numbers started to climb in late 2021, no one knew just how fast demand for parts and materials would rebound, and in the years since demand has continued to sky-rocket.
It’s an exciting time in the industry, which is buoyed by innovation and a drive to reach ambitious net zero targets, but this can make it difficult to forward plan.
When Airbus first announced plans to ramp up its A320 programme in November 2021, the supply chain reacted in shock. Could it be done?
Several years on, the ramp-up challenge is continuing to gather pace and manufacturers know that there are still significant risks and rewards ahead.
In an industry that had previously been used to 10-year production cycles, the last few years have shown positive signs, with deliveries continuing to increase pace reaching a high of 1,265 in 2023 – an 11% increase on 2022’s figures.
However ramping up has surfaced significant challenges in terms of both managing suppliers and improving operational efficiency. In particular, ramp-up situations can place extra pressure on internal teams, which if left unaddressed could compromise operational efficiency and lead to staff burnout. People management strategies designed to alleviate pressure must be part of their rate readiness planning. Will they succeed in meeting these challenges and, more importantly, will they be ready to make the most of the ramp-up opportunity?
2
How ramp-up ready are you?
For any OEM or top tier manufacturer, a rate readiness assessment should involve a close examination of their own process efficiency and operational performance.
The industry is littered with historic examples of businesses that have gone bankrupt during a rate ramp up either because they failed to understand that increasing volumes would not necessarily deliver profits, or that unexpected supply chain disruption would prevent them from meeting delivery targets. To truly understand their ramp-up capacity, manufacturers should undertake a comprehensive, internal review of their own operational performance, at the same time as looking externally.
“It’s easy to think that meeting the ramp-up challenge depends solely on the readiness of suppliers. While this is important, there is no point in investing resources in strengthening supply relationships and building in extra capacity if your own processes are under performing. To be truly collaborative, each business must look inwardly as well as outwardly.”
Alessandra del Centina, Managing Consultant, Vendigital
Taking an introspective look at internal processes can help to identify areas for improvement. For example, to support decision making, the following checklist should be considered:
Internal process checklist
• Is there sufficient capacity for now and the future?
• Is there a specific resourcing challenge?
• What investments, and associated timelines, are required to fulfil demand?
• Is there sufficient capacity for now and the future?
• Are you sharing the right information with key suppliers?
• Do key suppliers have long-term agreements and considerate payment terms?
• Are governance structures from the shop floor through the senior management operating efficiently? For example, are delivery challenges being escalated effectively to support rectification?
• Do you have the right KPIs in place to keep track of process efficiency?
• How effective is your machinery and equipment? Have you completed an Overall Equipment Effectiveness (OEE) assessment?
• Are there maintenance programmes in place for all production machinery and equipment?
• Are scheduling systems operating efficiently and are they scalable?
• Are support functions and systems in place? For example, can your quality and engineering teams support a higher demand?
“An accurate understanding of your own ability to meet demand targets is an essential starting point. You need to know how much of the demand you can fulfil in a range of supplier performance scenarios. This internal analysis must happen concurrently with a robust supply chain review to make sure all parties are delivering.”
Grant Millard, Director, Vendigital
3
A major A&D manufacturer’s perspective
For one major A&D sector manufacturer, responding to the ramp-up challenge required them to quadruple production output, from 18 to 75 value-added components per month, within a matter of weeks.
However, like many others, the business had experienced significant disruption during the pandemic, including a forced shutdown. Some workers had chosen to retire or switch careers in search of greater job security, and specialist skills were in short supply. In addition, the efficacy of some key equipment and tooling had been compromised due to a lack of investment, maintenance and use.
3.1 A holistic rate readiness assessment
The manufacturer knew that meeting the ramp-up challenge would require a high degree of operational efficiency and it decided to carry out a review of internal processes as quickly as possible, to identify any areas for improvement.
As well as looking inwardly, the manufacturer needed to know that its global supply chain was ready to meet the ramp-up challenge. With each valued-added component made up of more than one hundred parts and raw materials, just one weak link in its supply base could be enough to throw production off course.
To reassure the end customer that its ambitious production targets could be met, the manufacturer decided to take the initiative by asking its supply base: ‘Are you ready to ramp up?’
We couldn’t afford to get this wrong – our customer needed reassurance that we could deliver, and we needed the same reassurance from our suppliers. If we agreed to meet the ramp-up challenge, we would have to do just that. We urgently needed a data-led, end-to-end supply chain risk assessment to tell us if our suppliers were up to the job. We also needed to know that our own operational efficiency was back to where it was before the pandemic.”
A&D sector manufacturer
3.2 Mapping supply chain risk
A detailed analysis of the manufacturer’s supply chain was carried out to identify any risk factors that could disrupt its response to the rate ramp up for the A320 programme.
Data is key to developing a robust understanding of the risks and opportunities that exist within any industrial supply chain. As well as analysing shifting customer data, it is important to draw on diverse open source and cross supply chain data to get an accurate view of where demand is coming from; when and how much. In this case, Airbus had been clear about projected demand for the A320, so the manufacturer could plan ahead with a degree of certainty.
The project team at Vendigital conducted a holistic rate readiness assessment of the manufacturer’s supply chain, which involved analysing more than 100 individual suppliers operating out of countries in Asia, Europe and the US and gathering more than 10,000 data points.
During this initial mapping exercise, Vendigital considered each supplier’s performance over the past two to three years, including how they fared during past ramp-ups. This was combined with industry-specific data analysis, which provided further insights about each supplier’s delivery, quality and financial performance. The project team also spoke to industry contacts and sourced wider industry data related to any issues that might impact supplier performance in the future, such as commodity shortages.
Based on the findings of this initial mapping exercise, a total of 32 suppliers in eight countries were selected for further assessment based on a programme of in-person site visits and virtual meetings. Qualitative and quantitative data gleaned from these meetings was analysed to complete the rate readiness assessment, resulting in each supplier receiving a validated risk profile. Crucially, this risk profile wasn’t just based on the here and now, it also took into account where issues were most likely to arise in the future.
When assessing the risks and opportunities that might exist within a specific supply chain, it can be helpful to group suppliers by commodity. The most common risks relate to raw material supply, supplier capacity, production assets, tooling and skillsets, the supplier’s own sub-tier and operational performance. Throughout the assessment process, the project team also considered each supplier’s connectivity and how well they were using data to drive their own operational performance.
The final stage of the rate readiness assessment involved agreeing action plans with each of the 32 suppliers. These plans addressed areas such as load and capacity planning, KPIs, labour capacity planning, tooling and skillsets. With the help of a live digital tool to monitor the action taken by individual suppliers, the manufacturer was able to keep track of progress, and make strategic decisions about how to optimise supply chain performance for the long term.
By taking the initiative and working with their suppliers to prepare for the rate ramp up, the manufacturer is ready to capitalise on growth opportunities and has better visibility of issues that could arise in the future.
“The aim of the data-led rate readiness assessment was to identify both issues and opportunities that might otherwise have fallen under the radar. This 360-degree vision of the potential risks and rewards means that the entire value chain can meet the ramp-up challenge with confidence.”
Andrew Brough, Managing Consultant, Vendigital
3.3 Top 5 rate readiness insights
The top five insights from the rate readiness assessment carried out by Vendigital:
More than a third – 38% – of suppliers had inadequate processes for capacity planning
Analysis: Capacity planning – the assessment revealed a general lack of focus on capacity planning across the supply chain. In some cases, this was due to a lack of skills and, in others, new teams lacked knowledge of existing plant and machinery. If capacity planning was taking place, it wasn’t necessarily flowing down to machine level. Some suppliers were sceptical of demand projections.
One in five suppliers – 21% – lacked sufficient staff and urgently needed to recruit
Analysis: People – One in five suppliers lacked the skilled labour needed to meet the ramp-up challenge. This was primarily due to shedding staff during the pandemic although in most cases suppliers had worked hard to retain key staff.
19% of suppliers were experiencing difficulties with sourcing raw materials and products
Analysis: Supply chain – Some suppliers were unable to source the raw materials and components needed to meet the ramp-up challenge. In some cases, this problem had been made worse due to stocks having dwindled during the pandemic and ramping up inventory would take time and money.
12% of suppliers lacked tooling and equipment in production condition or needed to invest
Analysis: Tooling and equipment – Most tooling and equipment had been kept in production condition, but in some cases it had suffered due to a lack of use and maintenance. Some gaps in investment were also noted.
About one in 10 suppliers – 9% – had significant operational issues and were unable to ramp up production
Analysis: Operational performance – About one in ten suppliers were experiencing significant operational issues, which compromised their ability to ramp up production. Support would be needed to prepare them to meet the demands of market recovery.
4
How ramp-up ready are your suppliers?
As well as optimising their own operational efficiency, in a ramp-up situation all OEMs and top tier manufacturers need to know that their suppliers are ready to meet the challenges that lie ahead. Being prepared ahead of time could position the entire value chain for growth.
To find out if your supply chain is ramp-up ready, manufacturers should follow this step-by-step approach:
Understanding the ramp-up challenge
What
Do you know what the demand curve looks like? Over what timescale is it expected to take place? Can you quantify what it means for you? How will this impact your supply chain?
Tips
Having the ability to follow your Bill of Material to the first stage of production in supply chain will improve the effectiveness of demand sharing.
Initial assessment
What
Consider each individual supplier, gathering information about their performance during past ramp-ups along with other open-source industry data. Do you have access to analytical tools that can provide further insights about their delivery, quality and financial performance?
Tips
Current performance is a gauge of their ability to deliver current demand, small increases in the supply chain could impact even your top performing suppliers.
Prioritisation
What
Are some suppliers already feeling the pressure? Are others already rising to the challenge? Where issues have been identified, are they a problem now or could they become one in the future? Are some suppliers strategically important in a rate ramp-up situation?
Tips
Identify which suppliers would benefit from close management and further assessment.
In-person and virtual assessments
What
It’s important to meet with suppliers and see how well they are doing. Are there any gaps in their operating model? Are they short of skilled labour or tooling? Are the right processes in place?
Tips
Building relationships early and moving towards collaborative working will make information sharing more comfortable.
Action plan
What
Findings from in-person and virtual meetings should be analysed and validated. Suppliers are then given a risk profile and an action plan is agreed for delivery over a set time period. This action plan could consider factors such as load and capacity planning, KPIs, labour capacity planning, tooling and skillsets. Are you able to monitor performance against the action plan on a real-time basis?
Tips
This must be conducted in a way that builds buy-in from suppliers – if this is given as a top-down instruction, they will struggle to deliver the desired benefits.
People
What
Have you considered the pressure that the ramp-up will bring for people working within the supply chain? Is there anything you can do to alleviate this pressure and extend more support? Adopting the right management behaviours could help suppliers to maintain and attract the skilled people they need.
Tips
Due to the constraints affecting human resources within the sector, it is imperative to develop and protect the skill base.
Business as usual
What
Once a supply chain assessment has been completed and tools developed to help you to keep track of progress, manufacturers shouldn’t stop there. This focus on supply chain risk and reward should continue and become part of ‘business as usual’. Have you created feedback loops and set dates for reviews with individual suppliers? When will you be carrying out another holistic supply chain assessment?
Tips
This can’t be a one-off exercise and should continue to be reviewed on a consistent basis. Building key elements of rate readiness into day-to-day activities will help to develop your own teams’ awareness of the risks that the business is facing.
5
Realising the ramp-up opportunity
To make the most of a ramp-up opportunity, OEMs and top tier manufacturers should start by examining their own sales and operations planning process in detail to ensure everything is running smoothly.
It is vital that senior-level executives have access to the data they need to guide decision making as the ramp-up gets underway, and the use of automated tools and software can help to streamline and optimise processes. The opportunity to invest, collaborate with suppliers and develop relationships with customers could release significant future revenues and potential profits due to a strong order book and increasing market share.
The ability to plan ahead with confidence is critical in many industry sectors. Manufacturers can’t afford to sit back and wait for demand to increase; they need to plan with rate increases in mind. When sourcing components and raw materials, for example, leaving things too late could mean the business is forced to pay over the odds to secure shorter lead times. Better capacity planning would allow them to improve inventory management and make the right staffing decisions.
A data-led understanding of what it means to be ramp-up ready, both internally and externally, could help manufacturers to unlock opportunities to drive profits and improve operational resilience.
The mini case studies below highlight how we have supported businesses in the aerospace and defence sector to optimise their operations and realise the ramp-up opportunity.
Case study 1: Ramping up by improving Overall Equipment Effectiveness (OEE)
Task: The client wanted to optimise operational efficiency by reducing machinery and equipment downtime, which could undermine their capacity to meet ramp-up targets.
Solution: A data capture system was created to measure both up and downtime. Once collected, the data was interrogated to uncover any issues. The causes of downtime ranged from issues with set up to a lack of materials. An action plan was developed and implemented to resolve the issues identified.
Outcome: There has been a step change in OEE, and the manufacturer’s production backlog has been reduced by 75%. New internal processes around the maintenance of machinery have been put in place to further reduce downtime in the future and ensure that they are ready to meet the rate ramp-up challenge.
Case Study 2: Ramping up by changing order patterns
Task: The client was using fixed-demand period contracts that led to a ‘bull whip’ effect, where small changes at the top overloaded suppliers further down the chain.
Solution: To reduce the risk of supply chain disruption and prepare for the rate ramp up, a more collaborative approach was required. The manufacturer began building in ‘buffer stops’ to prevent orders from overwhelming suppliers further down the chain. A culture of collaboration was adopted which enables volumes to be increased over time rather than front-loading from the start.
Outcome: Improved supplier relationships across the value chain and the collaborative approach ensured that the supply chain moved in unison whilst working under pressure.
Optimise your operational performance
Related Insights
The UK’s aerospace industry has seen significant improvements in productivity but the truth is that much more could be achieved by accelerating the adoption of digital technologies and enriching the skills base.
Manufacturers need to collaborate closely with suppliers to mitigate the impact of shocks and supply chain disruptions.
The boom in Generative AI is creating new opportunities for aerospace and defence sector manufacturers. Used correctly, GenAI capability can help to optimise production processes, improve supply chain resilience, ringfence knowledge and reduce costs.
Subscribe to our newsletter