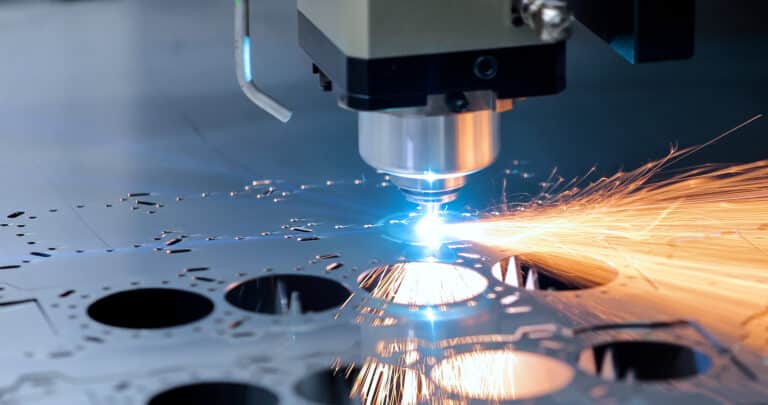
Putting factory-based production in the spotlight
Are manufacturers prioritising investment in digital capability and Industry 4.0 technologies?
In the realm of new product development, cost optimisation stands as a pivotal factor to ensure competitive advantage and desired profit margins. Every stage, from ideation to commercialisation, demands the management of resources to ensure competitiveness and profitability.
Amidst this quest, Design for X (DfX) methodology remains critical, offering a systematic team-based approach to optimise costs without compromising product quality or functionality. This blog delves into why employing DfX methodology is not just beneficial but critical for optimising costs during new product development projects. It is not uncommon to realise a 10-20% benefit by applying this best practice.
DfX methodology
Understanding Design for X Methodology
Before understanding its significance, let’s grasp the essence of Design for X methodology. At its core, DfX encompasses a spectrum of disciplines, each denoted by the ‘X’, representing various aspects like manufacturing, assembly, reliability, sustainability, customisation and more. It’s a proactive approach integrated into the design phase, focusing on optimising product attributes to align with specific objectives, whether it’s cost reduction, enhanced usability, or environmental sustainability. Like many aspects of good business, DfX requires balancing trade-offs to get the optimal product and requires a multi-disciplined team engaged in the process.
DfX methodology advocates for a holistic approach to product development, emphasising collaboration among multi-disciplinary teams right from the onset. By integrating stakeholders across design, engineering, manufacturing, and procurement departments, DfX facilitates concurrent engineering and can often breakdown departmental barriers. This collaboration enables early identification and mitigation of potential cost drivers, thereby preventing costly design changes downstream.
DfX framework
Design for Cost (DfC)
At its essence, DfX methodology revolves around Design for Cost (DfC), which entails optimising product designs to minimise manufacturing, assembly, and lifecycle costs while meeting performance and quality requirements. By meticulously analysing cost drivers, conducting value engineering exercises, and leveraging cost-effective design alternatives, companies can strike a balance between cost efficiency and product excellence.
Design for Manufacturability (DfM)
Manufacturing costs often constitute a significant portion of a product’s overall expenses. DfX methodology, particularly Design for Manufacturability (DfM), addresses this challenge by emphasising designs optimised for efficient and cost-effective manufacturing processes. By designing products with manufacturability in mind, such as minimising the number of parts, standardising components, and streamlining assembly processes, companies can significantly reduce production costs.
Design for Assembly (DfA)
Closely intertwined with DfM, Design for Assembly (DfA) focuses on simplifying product assembly processes. Complex assembly procedures not only increase labour costs but also raise the likelihood of errors and defects, further escalating expenses. Through DfA principles, such as modular design, self-locating features, and standardised interfaces, companies can minimise assembly time and labour costs while improving product quality and reliability.
Design for Reliability (DfR)
Product failures not only result in direct costs associated with repairs and replacements but also inflict indirect expenses like damage to brand reputation and customer trust. Design for Reliability (DfR) under DfX methodology addresses this by integrating reliability considerations into the design phase. By identifying potential failure modes and implementing robust design features, such as redundancy, error-proofing, and appropriate material selection, companies can enhance product durability and minimise lifecycle costs.
Design for Sustainability (DfS)
In an era marked by heightened environmental consciousness, sustainability has emerged as a key consideration in product development. Design for Sustainability (DfS) within DfX methodology promotes eco-friendly design practices aimed at reducing environmental impact throughout a product’s lifecycle. By incorporating principles like material recyclability, energy efficiency, and extended product lifespan, companies not only contribute to environmental conservation but also stand to benefit from reduced waste disposal costs and regulatory compliance.
Conclusion
In the competitive landscape of new product development, cost optimisation emerges as a paramount imperative. Design for X (DfX) methodology offers a comprehensive framework to achieve this objective by embedding cost-consciousness into every stage of the product lifecycle. Referring to the Should-Cost analysis throughout can keep teams focussed on achieving the target.
By embracing DfX principles like Design for Manufacturability (DfM), Design for Assembly (DfA), Design for Reliability (DfR), and Design for Sustainability (DfS), companies can unlock significant cost-saving opportunities while delivering innovative, high-quality products that resonate with customers. Ultimately, integrating DfX methodology isn’t just advantageous — it’s critical for navigating the complexities of new product development while maximising profitability and sustainability in the long run.
Take control of your costs – book a 30 minute slot with one of our cost transformation experts
Curious how you could accelerate the journey to cost reduction in your business? Book a free, no-obligation 30-minute consultation with one of our cost transformation experts to discuss your current operational challenges, specific ambitions and explore tailored strategies to achieve your cost reduction goals.
To benefit from our team’s deep operational expertise, simply click the link below and we’ll come right back to you.
Sign up to get the latest insights from Vendigital
Related Insights
Are manufacturers prioritising investment in digital capability and Industry 4.0 technologies?
With the government’s renewed focus on upgrading national infrastructure, clean energy providers must ensure their supply chains and processes are fully optimised ahead of any increased demand.
When it comes to new product innovation (NPI), there’s no such thing as a one-size-fits-all approach and engineers often find that juggling different priorities leads to costly, late-stage design changes.
Subscribe to our newsletter
Take control of your costs – book a 30 minute slot with one of our cost transformation experts
Book a free, no-obligation 30-minute consultation with one of our cost transformation experts to discuss your current operational challenges, specific ambitions and explore tailored strategies to achieve your cost reduction goals.