Introduction
As the world transitions to a low carbon economy, the mining industry is taking major steps on its road to Net Zero. Where precious metals demand is falling, demand for critical minerals (copper, lithium, cobalt, nickel) is rising at an unprecedented rate, fuelled by the global race to electrification.
In this series, we share industry insights, challenges faced in this new market space, and some of the work we’ve been doing across EV supply chain, New Product Introduction, and Cost Transformation.
Contents
1
The global race to decarbonisation
New Horizons
The global electrification journey has established itself as a key feature in the future of the mining industry, driven by government targets and legislation. Mining operators looking to meet Net Zero requirements have come across exciting and complex challenges. These range from developing a portfolio of new products, to securing the supply chain and strategic partnerships, through to establishing funding on capital investment requirements for the scale-up of new manufacturing and embed digital solutions within their operations.
The increase in demand for critical minerals coupled with the need to decarbonize and re-imagine the traditional operational model sees us entering an era of innovation, cultural change, calculated risk-taking and new merger and acquisition partnerships.
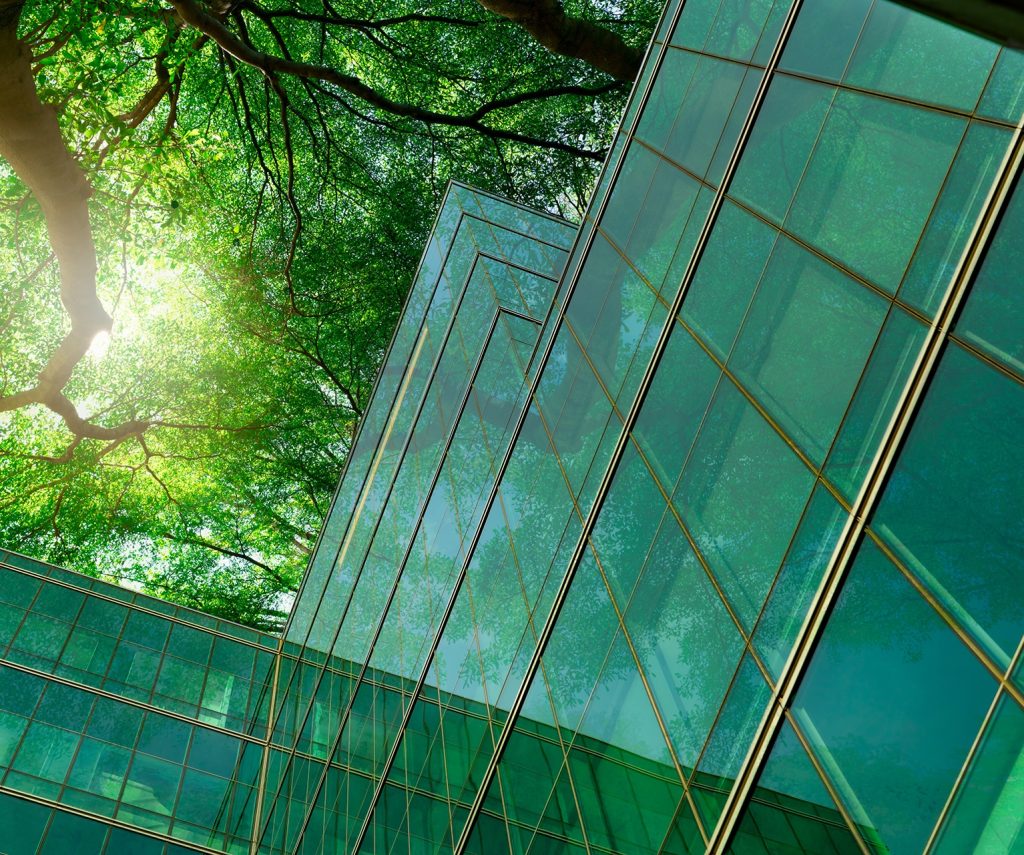
Over $17.8bn of budget allocated to decarbonisation for the below five mining companies
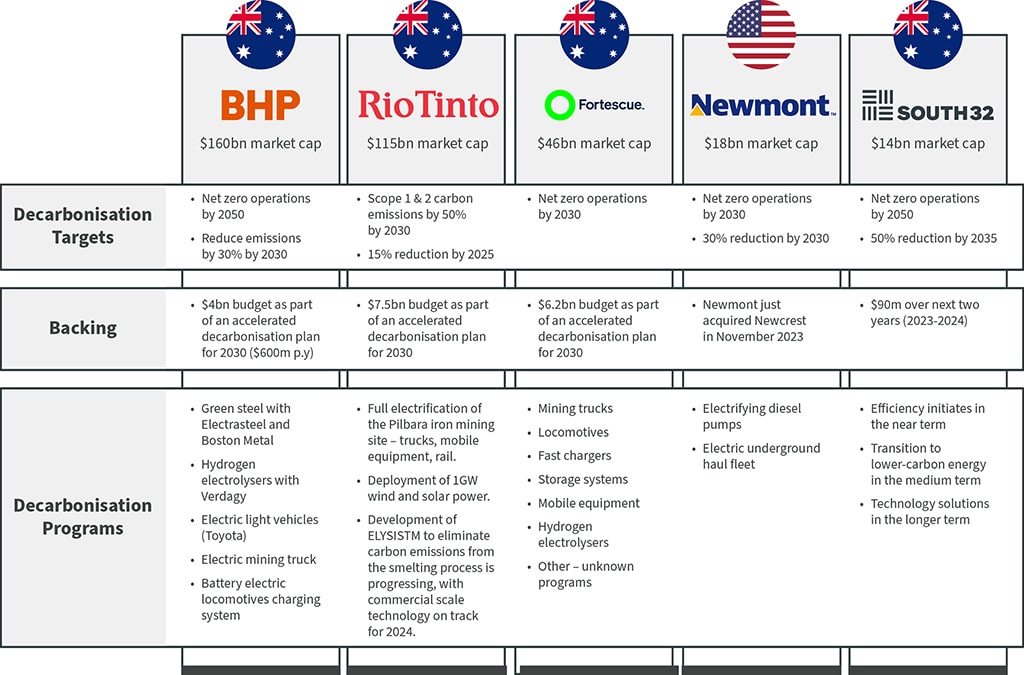
Over $17.8bn of budget allocated to decarbonisation for the below five mining companies
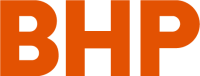
$160bn market cap
DETAIL
Decarbonisation Targets
• Net zero operations by 2050
• Reduce emissions by 30% by 2030
Backing
• $4bn budget as part of an accelerated decarbonisation plan for 2030 ($600m p.y)
Decarbonisation Programs
• Green steel with Electrasteel and Boston Metal
• Hydrogen electrolysers with Verdagy
• Electric light vehicles (Toyota)
• Electric mining truck
• Battery electric locomotives charging system
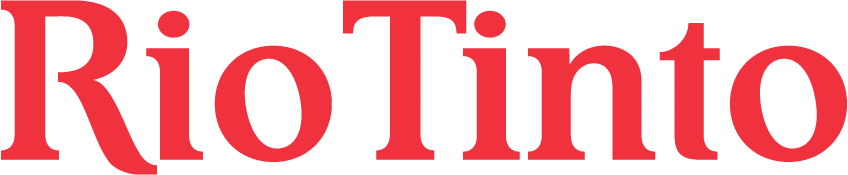
$115bn market cap
DETAIL
Decarbonisation Targets
• Scope 1 & 2 carbon emissions by 50% by 2030
• 15% reduction by 2025
Backing
• $7.5bn budget as part of an accelerated decarbonisation plan for 2030
Decarbonisation Programs
• Full electrification of the Pilbara iron mining site – trucks, mobile equipment, rail.
• Deployment of 1GW wind and solar power.
• Development of ELYSISTM to eliminate carbon emissions from the smelting process is progressing, with commercial scale technology on track for 2024.
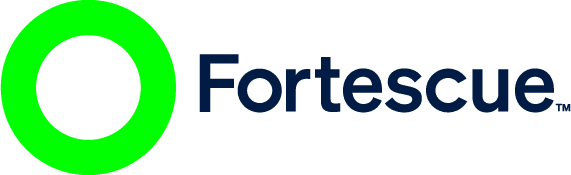
$46bn market cap
DETAIL
Decarbonisation Targets
• Net zero operations by 2030
Backing
• $6.2bn budget as part of an accelerated decarbonisation plan for 2030
Decarbonisation Programs
• Mining trucks
• Locomotives
• Fast chargers
• Storage systems
• Mobile equipment
• Hydrogen electrolysers
• Other – unknown programs

$18bn market cap
DETAIL
Decarbonisation Targets
• Net zero operations by 2030
• 30% reduction by 20300
Backing
• Newmont just acquired Newcrest in November 2023
Decarbonisation Programs
• Electrifying diesel pumps
• Electric underground haul fleet
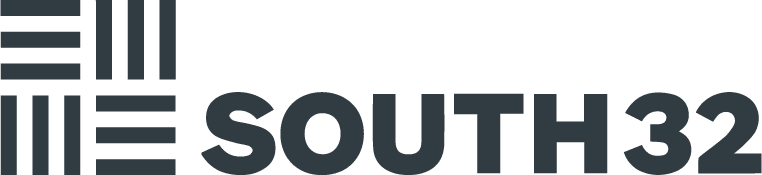
$14bn market cap
DETAIL
Decarbonisation Targets
• Net zero operations by 2050
• 50% reduction by 2035
Backing
• $90m over next two years (2023-2024)
Decarbonisation Programs
• Efficiency initiates in the near term
• Transition to lower-carbon energy in the medium term
• Technology solutions in the longer term
Key Statistics
of mining companies see local skills gap as the biggest barrier to adopting new technology¹
of leaders agree that the mining industry needs to consolidate to manage costs and risks more effectively²
increase in autonomous haul trucks in operation (760 to 1068)¹
agree that companies need to embrace new business models such as strategic partnerships, PE funding²
Net Zero by 2050 to achieve a 1.5C climate change target
1. https://www.miningweekly.com/article/tech-skills-shortage-an-existential-threat-to-the-global-mining-industry-2023-06-07
2. https://assets.kpmg.com/content/dam/kpmg/xx/pdf/2021/03/risk-and-opportunities-for-mining-2021-report.pdf
The road to net zero
There is no one-size-fits-all solution for achieving net zero emissions. Cell manufacturers are currently exploring various technologies including hydrogen, ammonia, and battery power, to decarbonize their equipment. However, like in the automotive industry, businesses will need to make strategic choices and commit to specific technologies for the long term. In the realm of battery technology, extensive research and commercial solutions continue developing at a rapid rate.
For instance, companies like Fortescue have acquired battery technology manufacturers and collaborated with equipment suppliers to convert existing diesel-electric assets to battery powered. On the other hand, BHP has taken a diversified approach, implementing both battery and trolley assist solutions for their mining trucks. Notably, BHP relies on its suppliers to commercialize solutions, while Fortescue is building the capability in-house. Interestingly, early adopters in the automotive sector initially favoured electric power as the future of mobility.
We’re now witnessing a growing trend towards hybrid solutions that combine hydrogen and electric technologies, particularly for heavy duty vehicles. Toyota for example, has invested heavily into hydrogen but now sees solid state battery vehicles overtaking their hydrogen vehicle sales by 2030. As alternative sustainable technologies become more cost-effective, businesses are adapting their strategies accordingly.
However, at some stage, they are going to need to “back” a technology due to the high capital requirements and extensive implementation timelines.
Regardless of the chosen technology for achieving net zero, businesses will face fundamental change. These include ensuring supply chain security, whilst transforming them to be more transparent and sustainable (including addressing Scope 3 emissions). This will come alongside optimizing and managing costs, acquiring talent, enhancing capabilities, and embracing digital and software solutions to reshape operations.
The road to net zero
Mine to inventory and the importance of decarbonisation
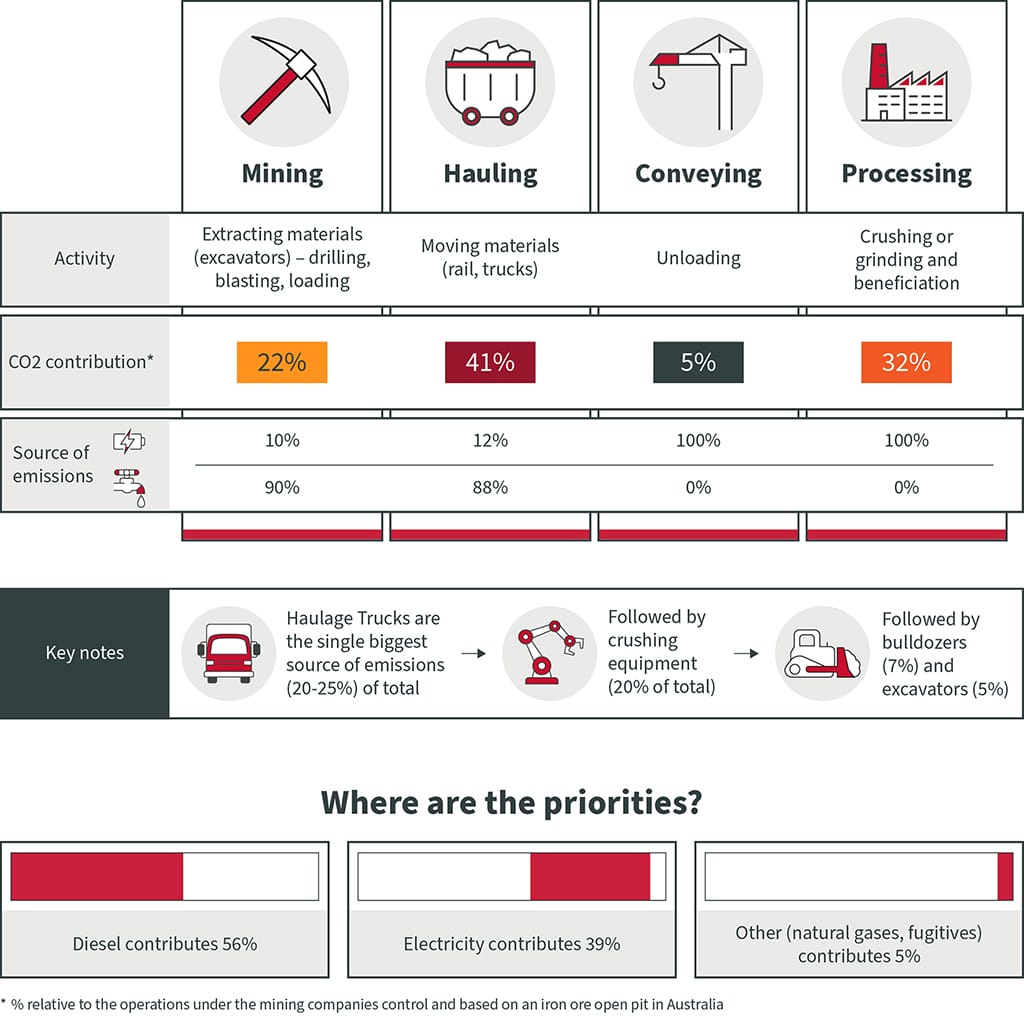
The road to net zero
Mine to inventory and the importance of decarbonisation
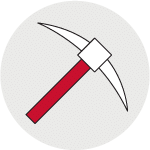
Mining
DETAIL
Activity
Extracting materials (excavators) – drilling, blasting, loading
CO2 contribution*
Source of emissions
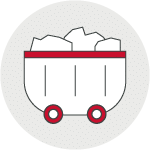
Hauling
DETAIL
Activity
Moving materials (rail, trucks)
CO2 contribution*
Source of emissions
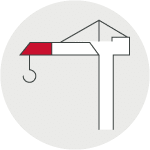
Conveying
DETAIL
Activity
Unloading
CO2 contribution*
Source of emissions
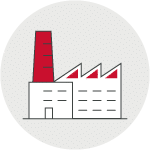
Processing
DETAIL
Activity
Crushing or grinding and beneficiation
CO2 contribution*
Source of emissions
Key Notes
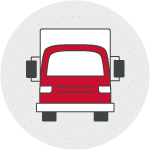
Haulage Trucks are the single biggest source of emissions (20-25%) of total
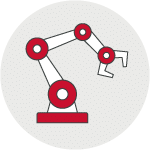
Followed by crushing equipment
(20% of total)
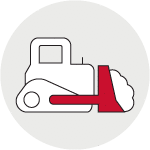
Followed by bulldozers (7%) and excavators (5%)
Where are the priorities?
Emission Contribution
*% relative to the operations under the mining companies control and based on an iron ore open pit in Australia
2
Procurement & Supply Chain
Shaping agile value chains to secure profitable routes to market; with cost engineering principles.
Labour shortages, port congestion, container availability issues, shipping costs, raw material shortages, and energy shortages have all disrupted supply chains in recent years. But this is a common challenge across industries. What sets mining companies apart, is the acquisition of capability through vertical integration to expand services from mine-to-port, to developing battery technologies and even setting up industrial scale manufacturing sites in which to produce them. Additionally, adopting electric technology comes with its lifecycle challenges – recycling is costly, and batteries need to be replaced often due to their health deterioration. Therefore, extending life through battery management systems and maximizing the value of the asset through second-life opportunities need to be at the forefront of the strategy to remain cost competitive. However, to achieve this, the right partnerships in the value chain are needed.
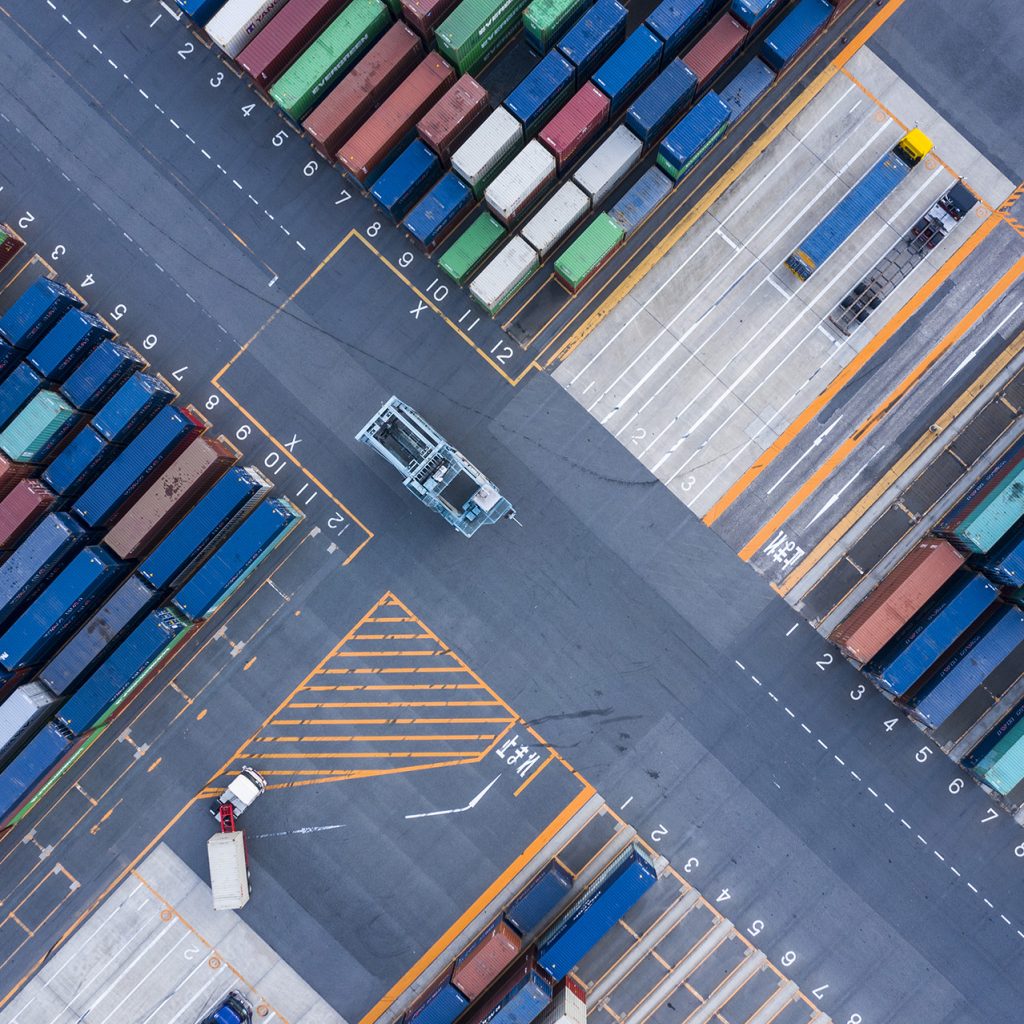
Resetting the supply chain
It is key that organisations do not lose sight of building the right procurement function and team to get spend under control quickly, particularly in the midst of New Product Development. Traditional capital project procurement will need to be expanded to include strategic product procurement. Close collaboration with capable suppliers will be needed. Doing so will allow organisations to be successful with ESG initiatives, cost transparency, co-development and smart contracting for agile, scalable, and sustainable supply chains. In addition, demand for manufacturing and smart technology has created additional risks in the supply chain in terms of securing capital manufacturing equipment, leaving many organisations tied to Asian markets. Decades of supply chain globalisation has introduced dependency on low-cost country sourcing to deliver profitable growth and healthy margins. However, it has come at an alternative cost: the erosion of local capability in manufacturing and a decline of skilled workforces across sectors.
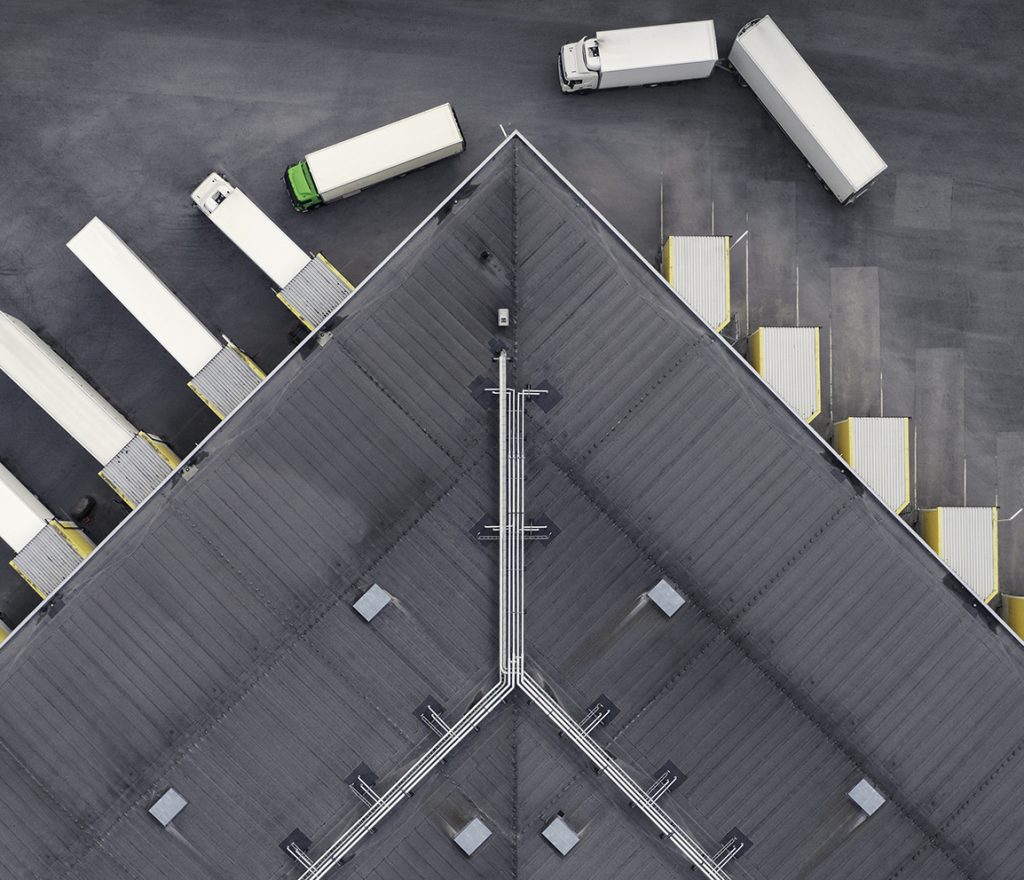
Empowering Procurement
Procurement professionals in this space are going to enter an exciting and challenging new phase as they seek to develop and establish suppliers that can help their organisation with innovative solutions and entering the market in a cost conscious and secure way. Much investment will be riding on having the right procurement and supply chain outcomes. The need for both innovation and capabilities is giving rise to an increasing number of partnerships and joint ventures between mining and engineering companies. It allows them to capitalize on knowledge and capacity as organisations seek to leverage experience to de-risk their supply chain and route to market with a level of cost consciousness. Getting early supplier (and procurement) involvement, establishing more partnership agreements, and tapping into developing expertise with careful timing and planning will ultimately help shape successful outcomes for both buying and manufacturing scalability.
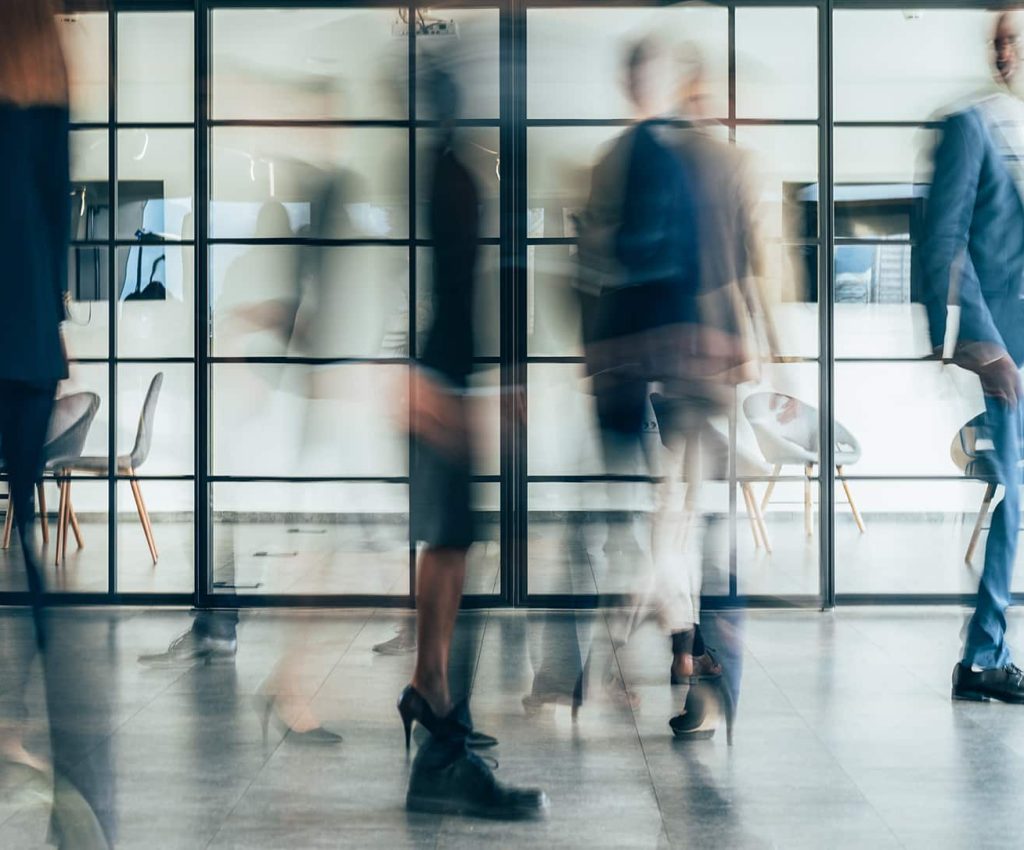
Deals
The global mining market witnessed deals worth $121 billion in 2023, which is a 75% growth compared to 20223. Deal activity is heating up for companies who want to take advantage of the rising demand for critical minerals. With any M&A, companies will need to ensure they have the right governance, structure and due diligence processes in place to manage profitability and maximise knowledge sharing to leverage synergies.
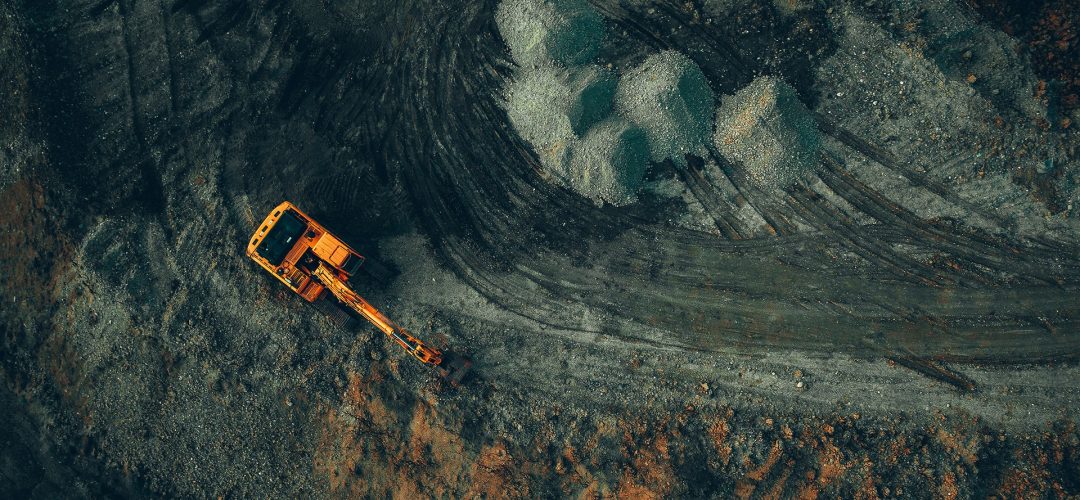
3
Cost & Value Engineering
Maximising the lifetime value of assets through Cost Engineering & Design for Excellence Principles
Manufacturing methods, servicing in the field, and the safety of electrified assets are some examples of what needs to be considered in the development of these products by mining companies. It is not enough for these to be a checklist upon design completion, however. For cost to remain under control, legislation to be adhered to, and competitive advantage to be secured, they must be ingrained into the product development process early on – right from the concept phase. This can only be done by ensuring the engineers designing these products have the right cross functional intelligence, framework, and team culture to drive these considerations from the start right through to production.
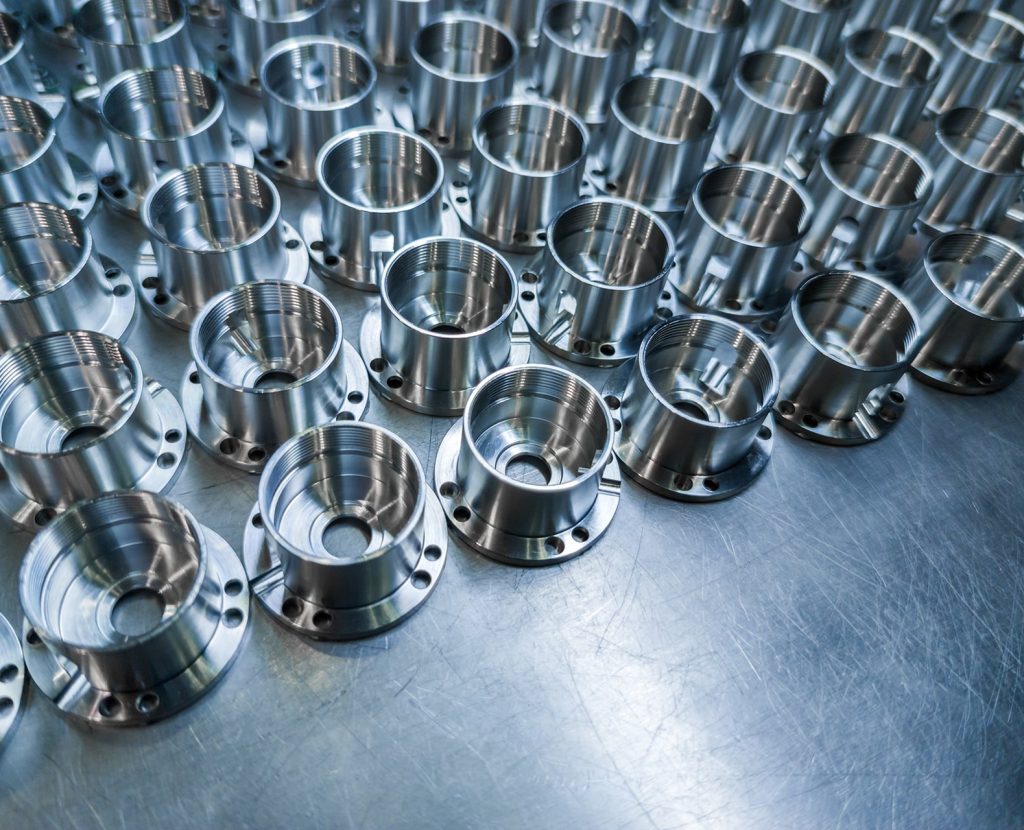
Design for eXcellence (DfX)
As organizations increasingly focus on product innovation and cutting-edge development, cross-functional collaboration becomes paramount. Subject matter expertise should be engaged early and consistently during product development. This approach ensures that critical aspects related to cost, quality, and safety are addressed when shaping design concepts. Cultivating a Design for Excellence methodology is essential for successful adoption of innovative technology. One must not forget that battery systems come with complex integration systems such as e-motors, cooling systems, fire suppression systems and other systems that work together
as a powertrain system.
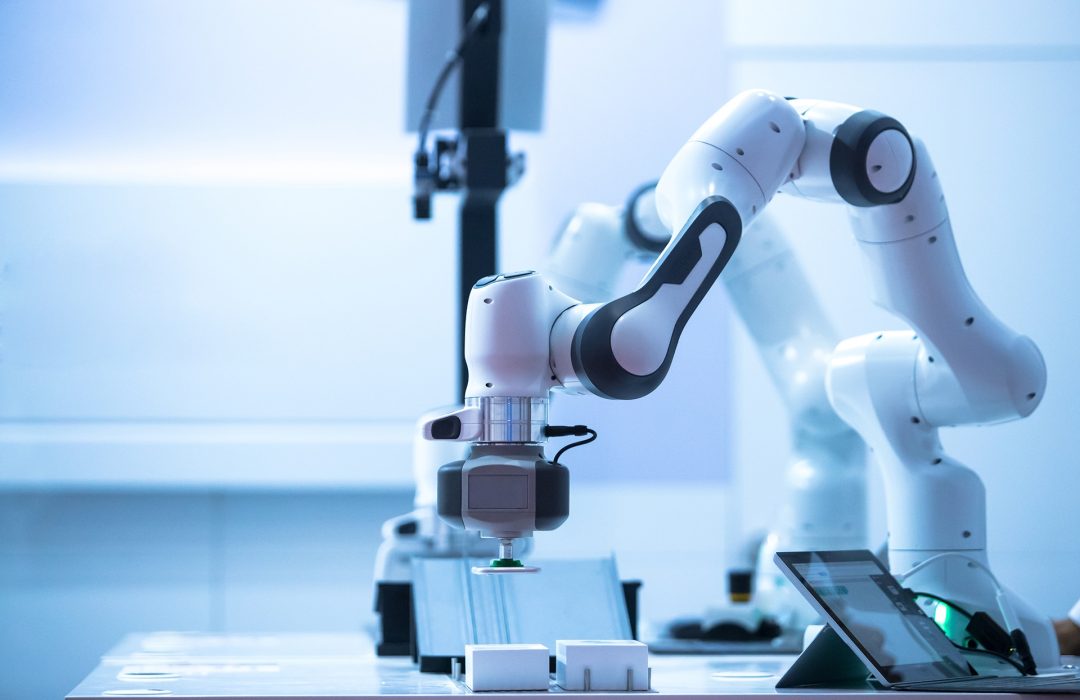
Cost management
Electrification comes with high capital and product development costs. As organisations look to break-even in the short term through asset conversions, product cost management (Cost of Goods Sold) will be high on any CFO’s priority list. A detailed level of cost detail broken down to first principles will set the market leaders apart from the followers and ensure long term profitability. This can be achieved using methodologies such as Should Costing and Target Costing to determine the achievable product value through forensic analysis of its lifecycle – from the raw material costs, to the suppliers manufacturing costs and in-service maintenance costs.
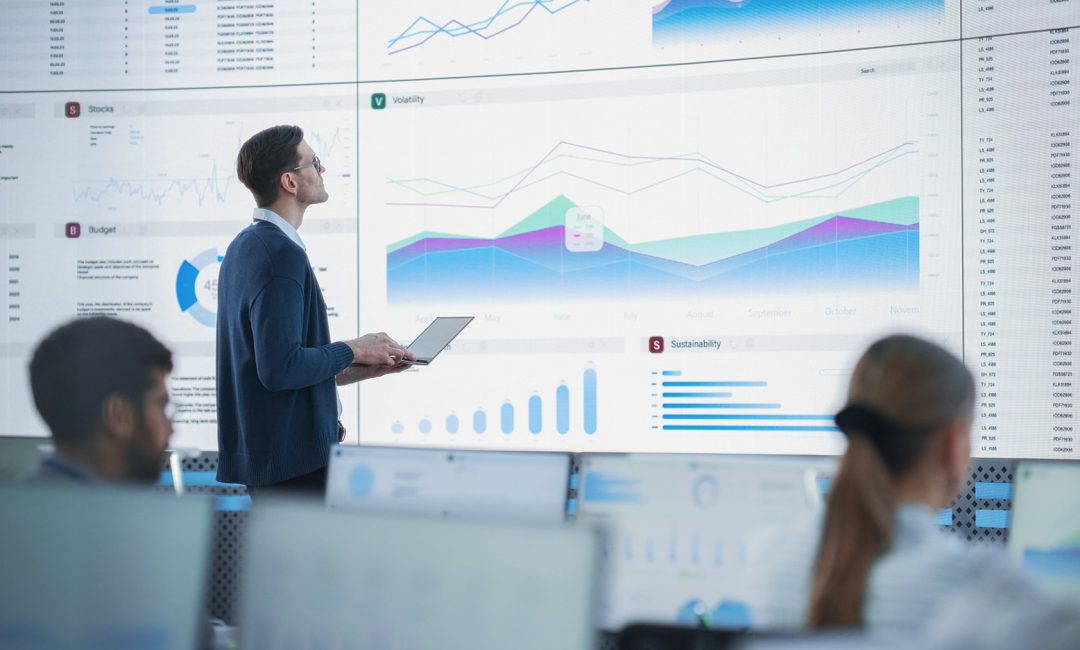
Product Decarbonisation
Whilst electric vehicles are zero emissions at the tailpipe, it is widely acknowledged that their production is more carbon intensive than traditional Internal Combustion Powertrains. This means that OEMs must work even harder to identify and implement levers throughout their supply chain to move towards a true zero emissions state. For instance, using cost engineering methodologies to identify the most energy intensive production processes, then working with the part manufacturers to pinpoint sustainable alternatives. This could be achieved through activities such as investing in more lightweight technologies, identifying more energy efficient materials, or improving the carbon footprint of the factories supplying the parts.
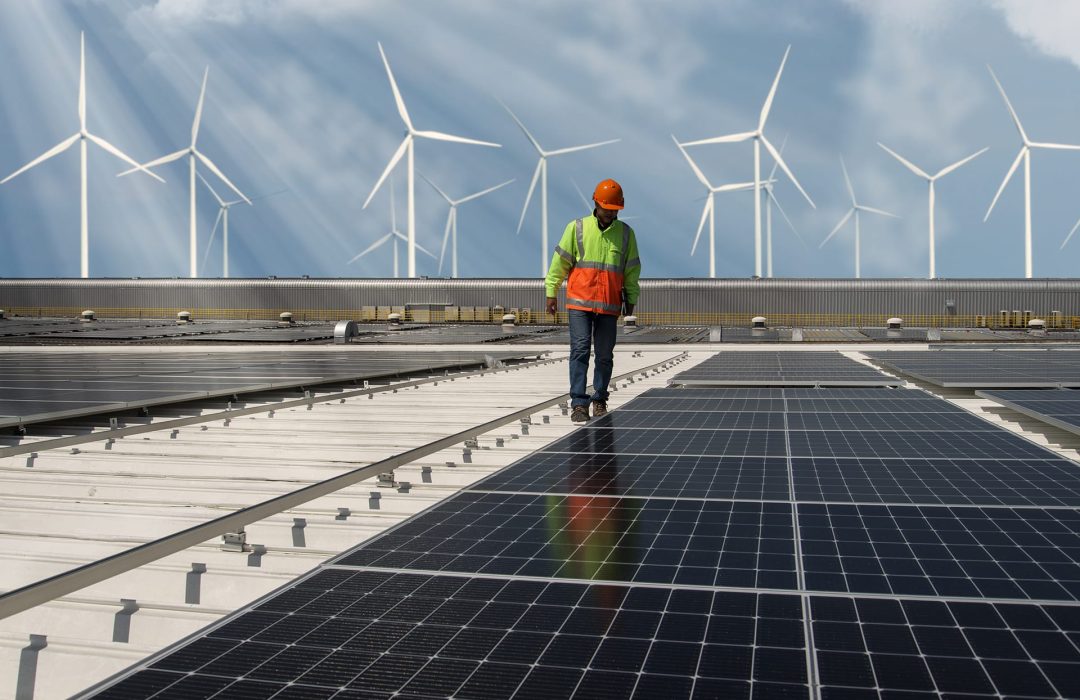
Identifying benchmarks
Competitor analysis or benchmarking is crucial for positioning products in the market. By obtaining and dissecting competitor products, businesses can challenge design concepts and test ideas with their supply chain. Strategic market positioning hinges on these activities.
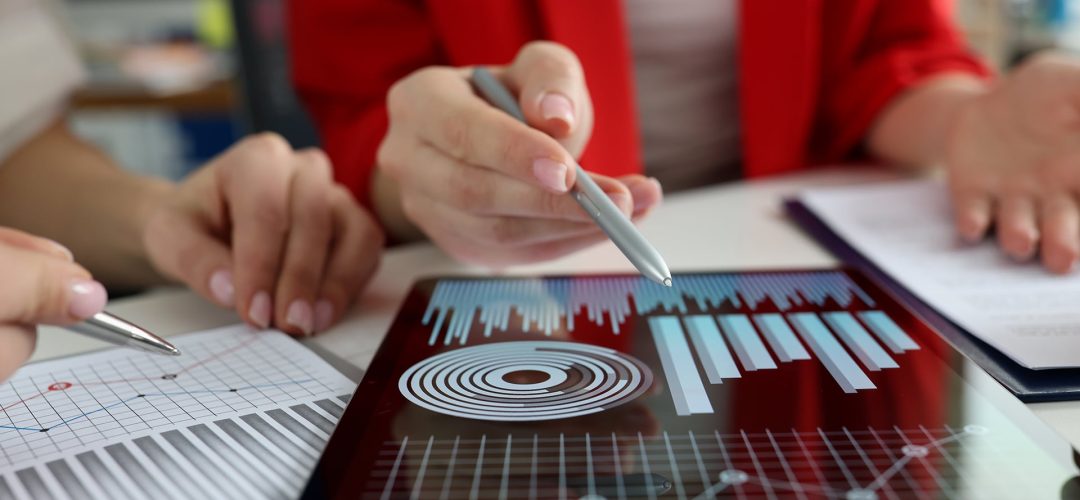
Gap analysis and Cost Control
A Gap analysis is a direct comparison of all the features of the product cost between the original Should Cost and the latest supplier quotation. It is the forensic detail in the Should Cost that empowers procurement teams to prepare for negotiations through fact-based intelligence. By understanding the cost drivers and opportunities to close a cost gap, procurement will be able to incorporate the right commercial models with their suppliers to enable continuous improvement and drive long-term cost-down activities.
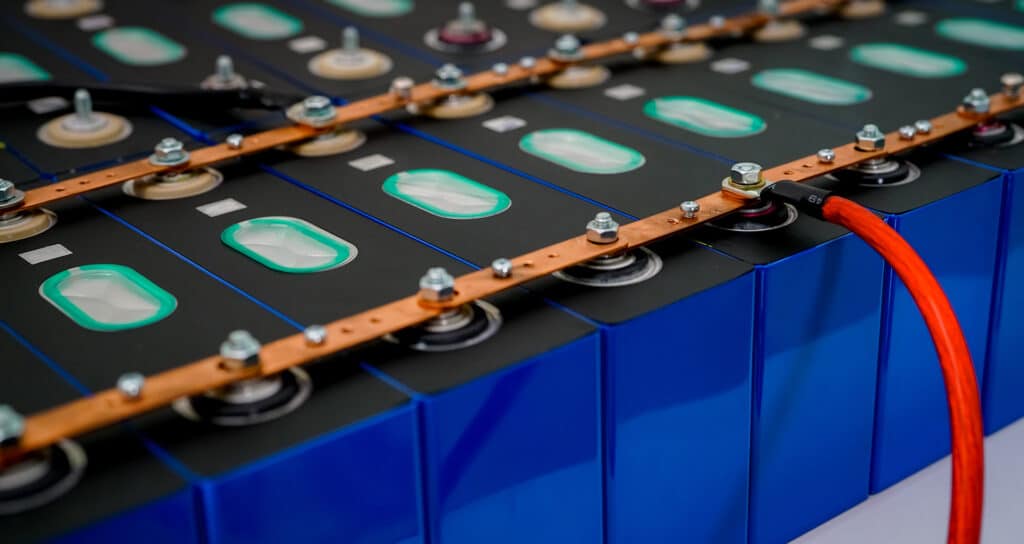
4
Operating Strategy
Navigating challenges in mining scalability; with cost engineering principles
The transition to net zero emissions will necessitate increased mining activity, rather than less. As we rapidly scale up low-emission energy systems, (solar and wind power, electrified equipment and grid-scale batteries, etc.) the demand for raw materials will surge. Meeting this demand will require certain leaps of faith across internal operations and the supply chain.
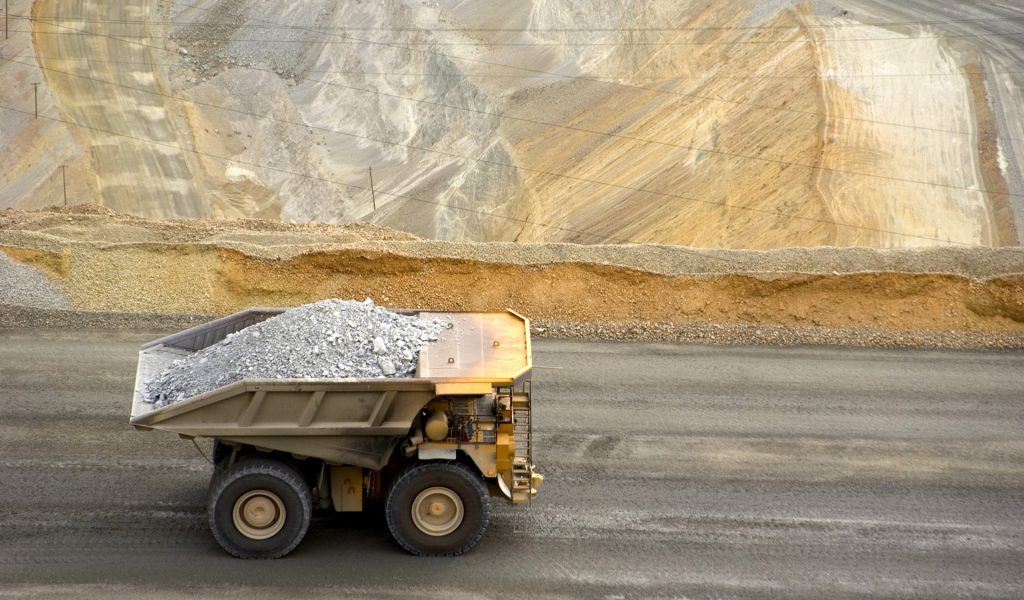
Vertical integration
As the world grapples with the need for a secure supply of critical minerals to support the transition to sustainable energy, there is an intense competition for capacity among critical suppliers. While some mining organisations are relying on their partners to scale up manufacturing and innovate to meet demand, others are taking a bold step by acquiring their suppliers to secure capability and capacity. For an industry not accustomed to product manufacturing, this shift introduces a host of new challenges related to engineering, manufacturing, testing, procurement, and quality control.
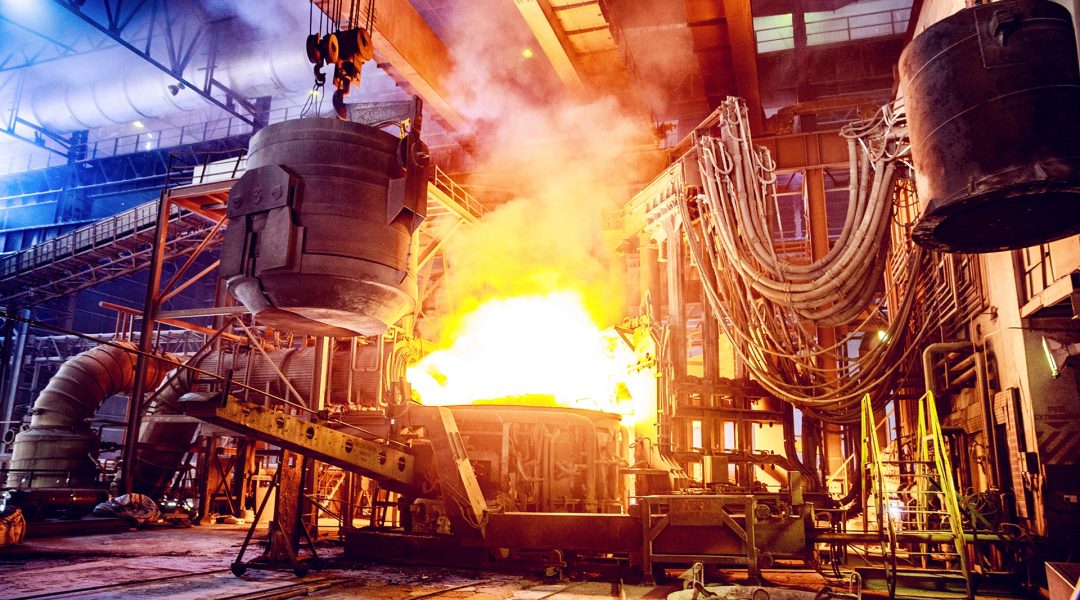
Resource scarcity
Ore resources are limited, and companies will face more complex deposits and jurisdictions to navigate, which could mean higher operational costs. Companies will need to become leaner, cost-conscious, and invest further in technology to improve operational output efficiency. This may require developing mine sites in a more modular and dynamic way, where assets can simply be re-used and transported.
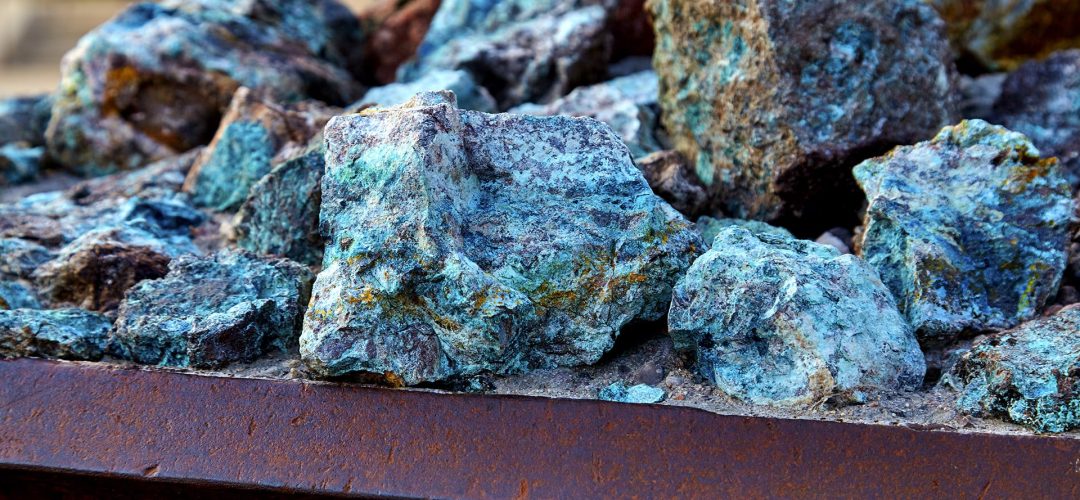
Technology Piggy Backing
Several companies have forged partnership deals with high-volume manufacturers such as Tesla (BHP Nickel West – Tesla) and General Motors (Wabtec & GM on Ultium Batteries) to improve economies of scale and enhance their bargaining power in securing critical supplies. These collaborations typically hinge on a core product developed by the automotive manufacturer, while the lower-volume partner creates an applicable product tailored to their specific needs. This process demands cross-functional capabilities that may not currently exist within mining companies. Consequently, there is a growing need to attract talent from other product-focused industries and implement robust product development programs, which adds complexity to operational management.
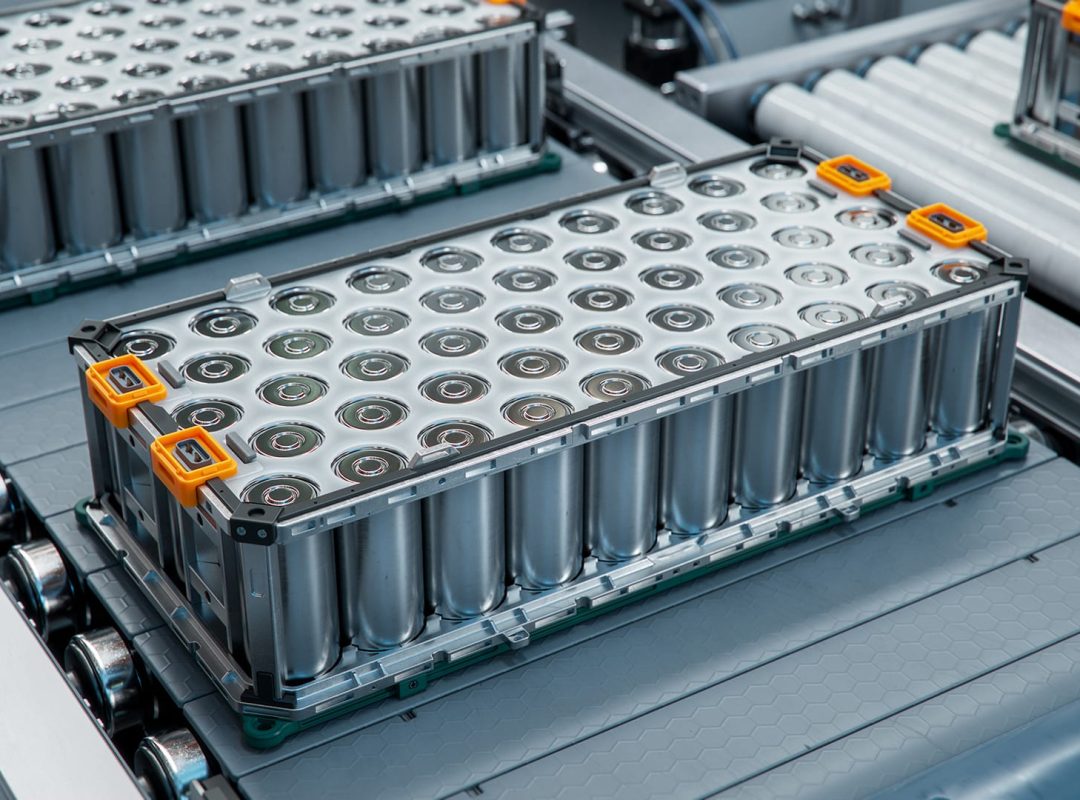
Talent and capability
With automation in manufacturing only addressing a fraction of challenges in capability, ramping up manufacturing across new technologies will initially have a lower throughput. To improve the maturity of production, a whole host of new capabilities are required around battery design, industrialization, equipment calibration and maintenance. Mining companies will need to collaborate with local government to accelerate investment in qualifications, and training to develop the skills and knowledge needed across the battery lifecycle in areas like innovation, production, and in-vehicle maintenance. This will be imperative to supporting nearshoring of EV production and refurbishment as batteries require frequent replacement. Otherwise, consumers could face the impact of higher-costs of goods imported through a carbon intensive supply chain.
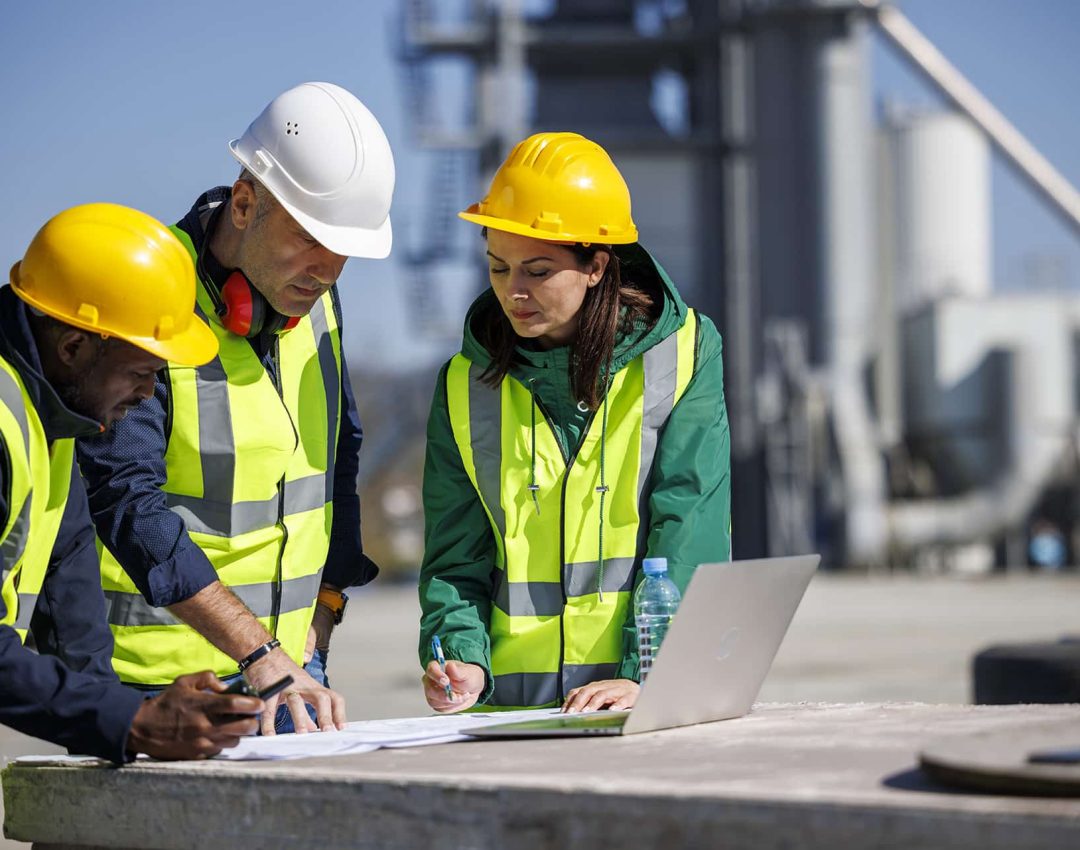
Technology Maturation
Moving away from outdated legacy systems and process is essential for achieving scalability and sustainability goals. Mining companies need to embrace digital technologies for efficiency gains such as data analytics, automation, AI and ERP systems which include product development and management.
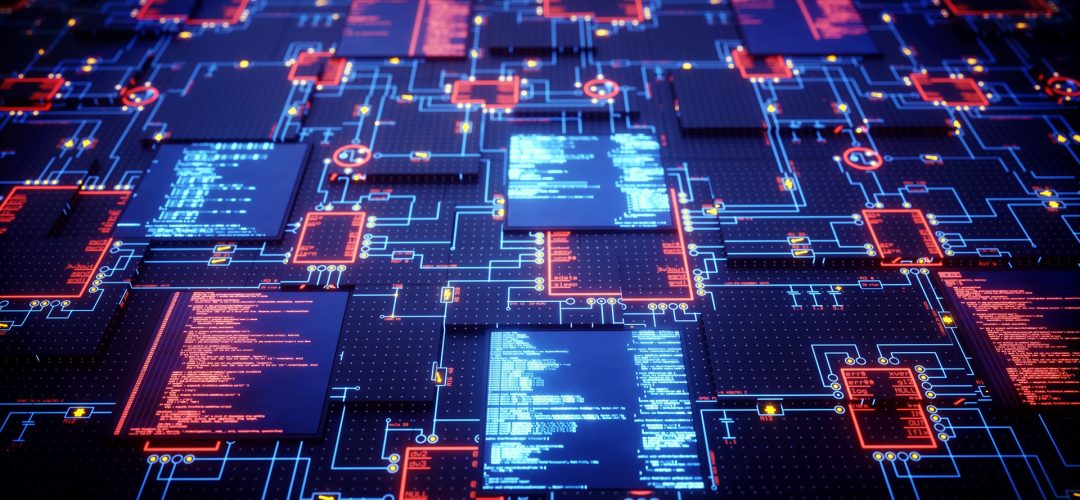
5
Key Considerations
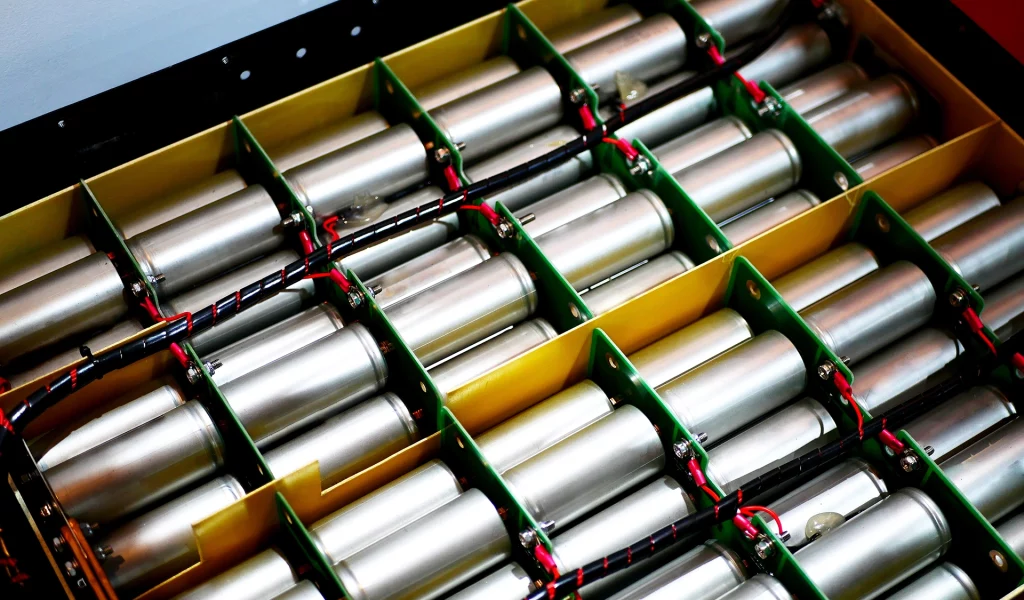
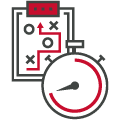
Strategy is Fundamental, but timing is everything
• Evaluate opportunities to own more of the supply chain or partner with OEMs to piggy-back on commercialised technologies
• Ramp up capability within electrified solutions and other sustainable alternatives
• Transform teams to become product focussed, rather than project focussed solutions
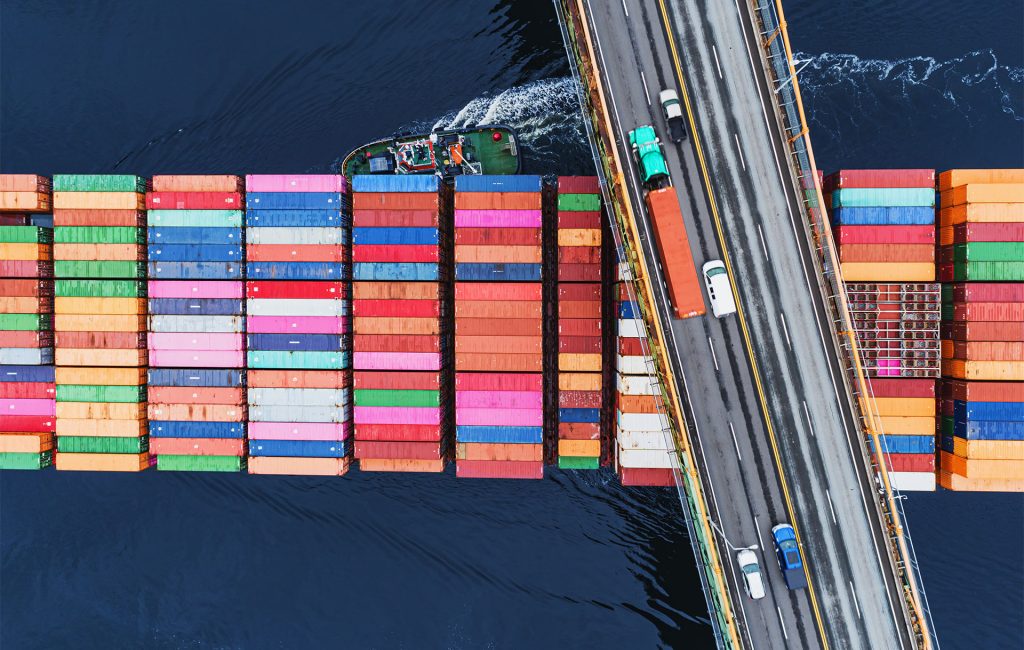
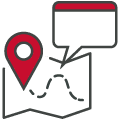
Take advantage of the supply chain
• Early supplier involvement and collaboration will be key to improving knowledge and identifying risks and opportunities with new product introduction
• Setting up the right process and tools to assess the supply chain is crucial to making the right supplier nominations based on cost, quality, delivery and sustainability
• Smart contracting to leverage supplier know-how and improve designs for reliability, manufacturing, aftermarket, maintenance and overall cost of ownership
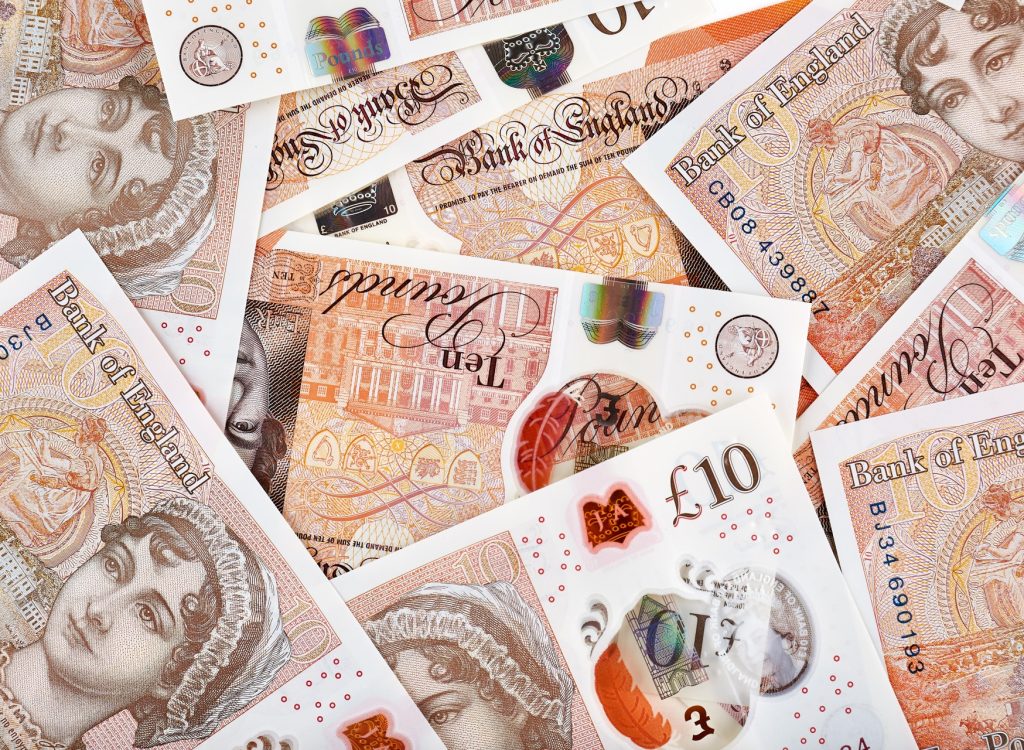
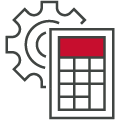
Cash is King
• Ensure you have the right cost control mechanisms in place to pro-actively address product and commercial opportunities and risks
• Utilise cost engineering as a means of forensic analysis on key purchased equipment to identify material, process, and capital cost down opportunities
• Continuously review exposure to critical mineral needs for the energy transition and set up supply chains to mitigate potential bottlenecks
• Evaluate new revenue making opportunities through the adoption of sustainable solutions, such as second lifing, Solution as a Service models or by supplying modular battery packs to other industries
6
Creating certainty around business growth
Five steps to creating certainty around business growth
Five steps to creating certainty around business growth
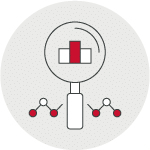
01 Discover
DETAIL
Design to Cost (Dfx) with comparative benchmarks on materials, design, and production scalability + understand capex and opex costs, macro factors
Detailed operational strategy including investment phases
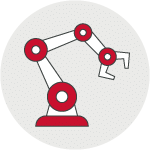
02 Establish
DETAIL
Understand potential operational costs with modelling of product process step including bottlenecks, downtime, processing time and lifecycle costs
Construction funding stage: Digital factory simulation to establish design and layout
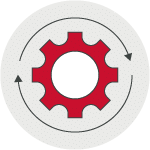
03 Stabilise
DETAIL
Forecast and maintain ROI profiles through procurement spend analytics and solutions such as virtual commissioning and ramp up + factory planning
Introduce more intelligence and automation through scalable IT infrastructure
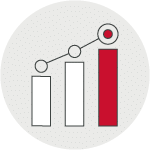
04 Grow
DETAIL
Start optimising OEE and throughput with clarity on asset performance, management and establish maintenance plans
Recalibrate commercial structures, supply chain and supplier performance for growth and sustainability
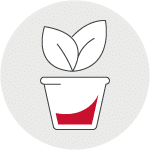
05 Mature
DETAIL
Review on-going costs, price-points and product profitability
Study of next gen product innovation and lifecycle management
Capex and Opex review, cost optimisation and reinvestment in innovation
7
Conclusion
With mining companies committing to decarbonise by 2050 or sooner, and in the backdrop of increasing customer pressure for greener products and solutions, the whole sector faces pressure and incentive to decarbonise their operations.
Latest projections estimate an investment between $100m – $130m to decarbonise a 25million metric-ton facility, and there is real work to do to identify technology that can secure this ambition in both the short and long term, with many players in this sector actively building decarbonisation in their mission statements and forward strategy.
The mining sector needs to strike a balance between its economic and material contributions to other sectors such as automotive and renewable energy that are also looking to decarbonise through battery technology, whilst assessing and minimising its own environmental impact and carbon intensity.
Over the next few years, we will see some incredible cross-overs in sharing greener technologies across industries that can ultimately pave the way for a cleaner future.
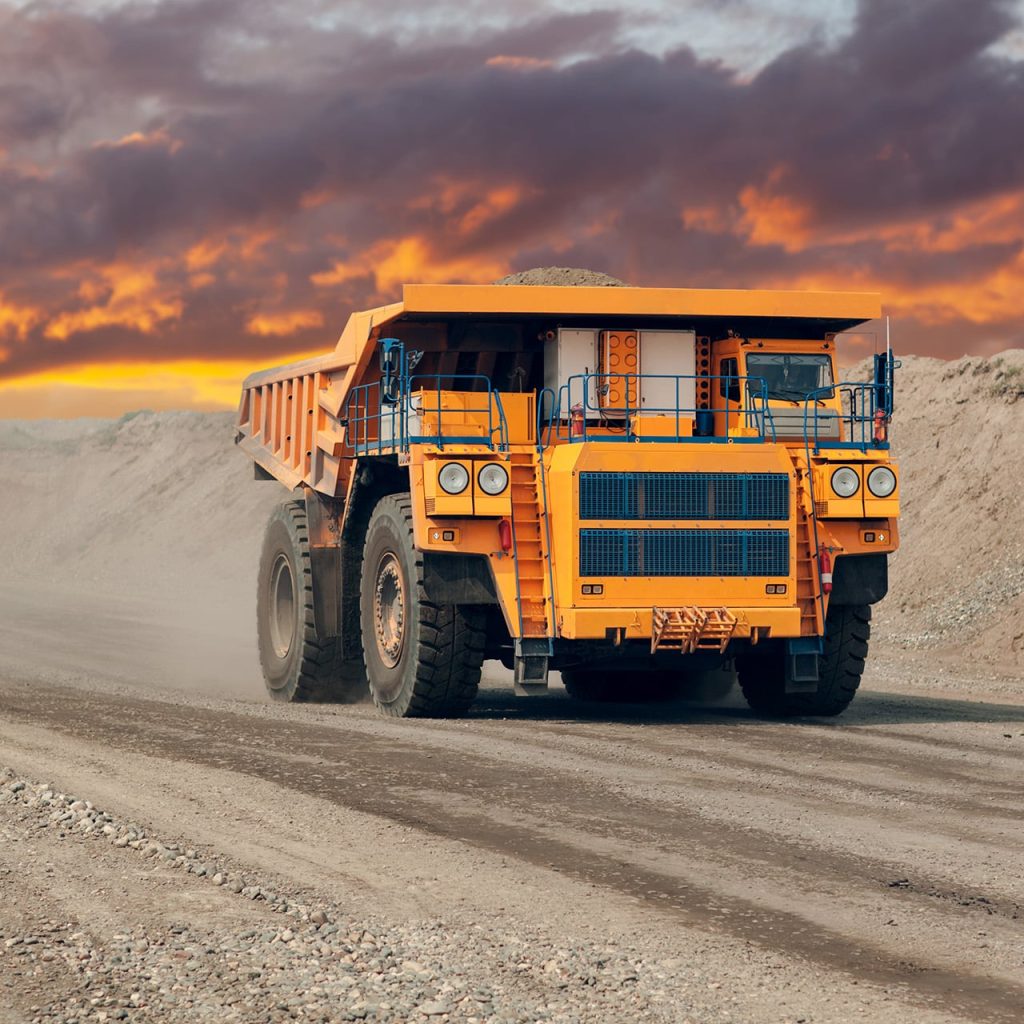
Authors
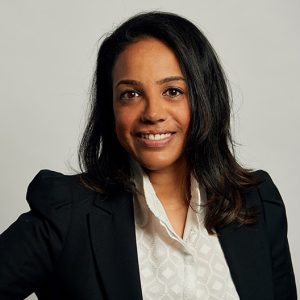
Sheena Patel
Director – Automotive
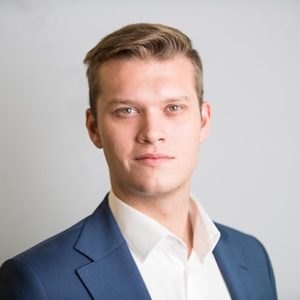
Martin Pochopien
Managing Consultant
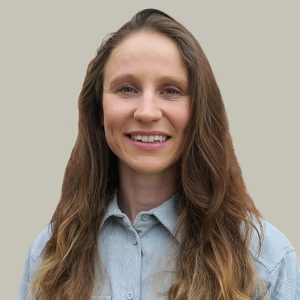
Marie-Louise Kertzman
Senior Consultant
Explore Vendigital