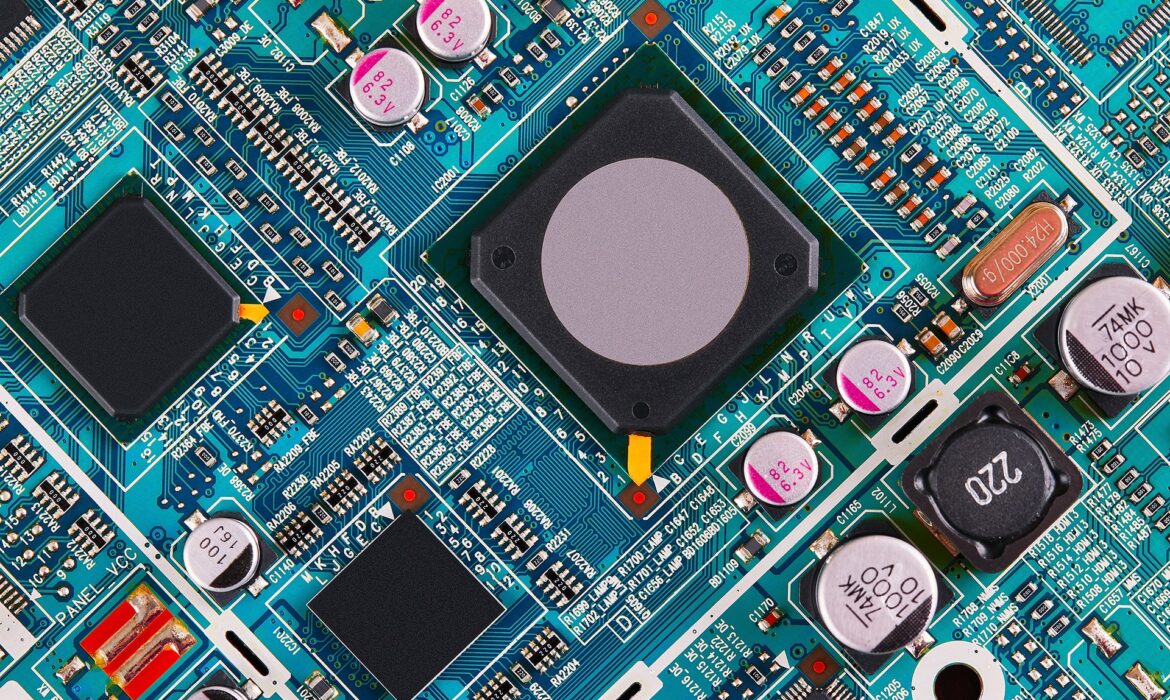
The electronic components market impacts you – knowingly or not
Today, in pursuit of greener and cleaner technologies, we are seeing significant step changes in the application of electronic components and digital technologies across a variety of products and portfolios that have been traditionally mechanical in nature. With increased automation and use of data intelligence to enhance product performance, these expontially advancing commodities continue to be harnessed in almost every aspect of everyday life.
The automotive sector is a perfect example where electronics play a huge role, even though the vehicle manufacturers rarely purchase electronic components and/or PCBAs themselves. Taking the average car as an example, in 1970 an estimated 5% of the total cost of the vehicle was related to electronics. That figure has increased to 35% by 2010 and is expected to reach 50% by 2030¹.
Historically, most vehicle manufacturers chose to outsource electronic assemblies as “build to specification” or “black box” products in order to reduce in-house design complexity as well as capital investments to manufacture. This resulted in the growth of some of the largest OEM suppliers in the world, such as Bosch, with €56.4b annual revenue in automotive sector (2023 data)².
The “black box” purchasing strategy, although successful in the past, results in significant blind spots for the end vehicle manufacturer. To fully identify and explore sector risks & opportunities, vehicle manufacturers had to change their approach and increase both their understanding as well as involvement in the electronics sector.
One of the great examples of that shift is the novel approach to power electronics, such as inverters.
Contents
1
The growing demand for Power Electronics and the inverter value chain
To fully grasp the complexity and challenges in the specific area of Power Electronics, the key design elements and value chain elements need to be understood. The diagram below shows the simplified value chain of an average automotive Silicone Carbide (SiC) inverter, focusing on the electronic elements.
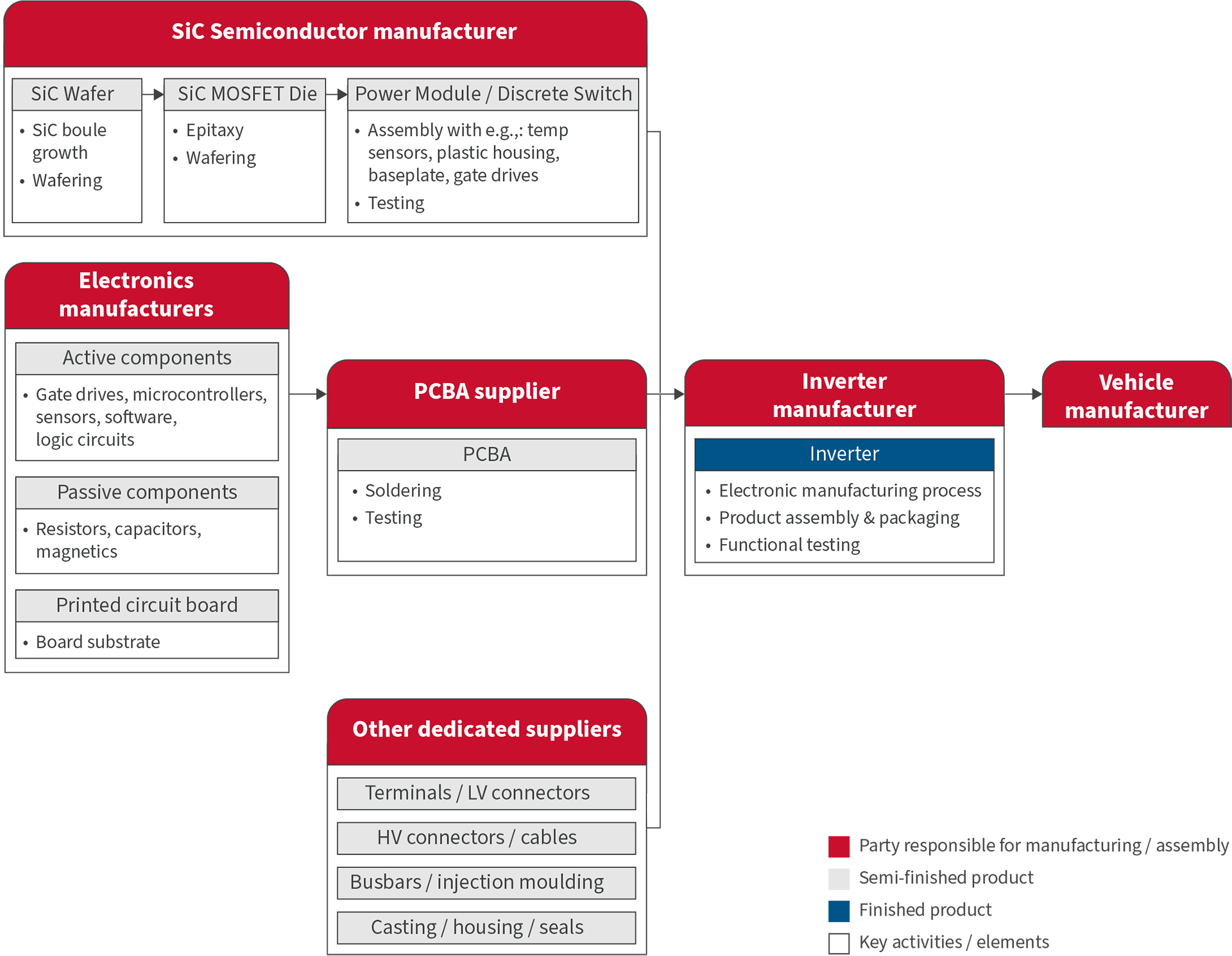
In general, components making up an inverter can be split into 3 groups:
Power Modules / Discrete Switches
The heart of an inverter and the element responsible for switching the flow of the current to transform DC into AC voltage. Discrete switches require further work by the inverter manufacturer to fully implement the switches, such as appropriate control system and cooling. Power Modules typically contain several discrete switches and are integrated with a cooling base plate. They tend to be easier to implement, although offer less flexibility in terms of design adaptation.
Switching elements are manufactured in stages as wafers, dies and finally switches and require specific manufacturing processes as well as technology. Typically, new manufacturing plants / lines take 2-3 years to launch and reach full capacity.
Standard electronics & PCBAs
Mostly utilising the industry standard, off-the-shelf components, assembled by established PCBA suppliers. Despite these components often being dedicated to a specific sector, global shortages can often impact the availability of materials.
Other non-electronic components
Typically sourced in line with established category strategies and requiring relatively low investment, include components such as aluminium die-casted housings or overmoulded busbars.
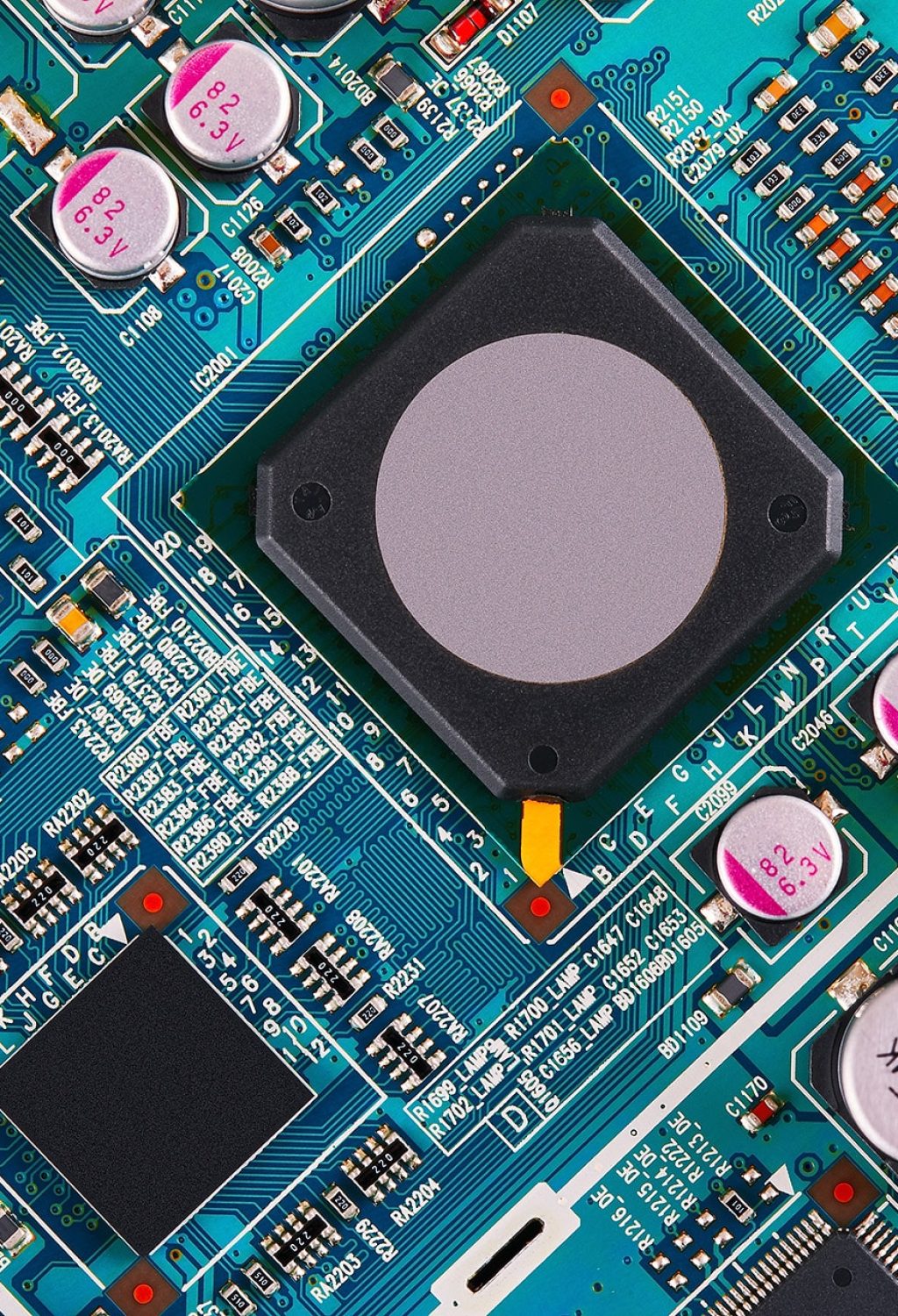
We see today that automotive power electronics is a unique area within the electronics market, which has grown rapidly over the last couple of years. With the sector having been very limited with low-volume BEVs and fewer hybrid vehicles in the early 2000s, we have seen it grow to a market size of up to $8.3bn in 2020³, and continued growth with a ~4.7% CAGR4.
The growth of this market has been largely equated to an increased significance of EV Inverters – a critical technology in powering e-motors; using energy from the conversion of DC to AC voltage in batteries. It is a critical element of any EV powertrain, and its efficiency and performance directly impact the overall performance of the vehicle.
Undoubtedly, one of the most important elements of the inverter are the power switches – the design and limitations of the switches themselves will determine the performance output of the end product. Depending on used technology and final product design, the power switches could make up to 40% of the cost of the inverter.
As we’ve seen rapid growth from the early 2000’s through to present day, manufacturers around the globe began to reach their capacity limits. As such vehicle manufacturers were faced with a new set of challenges; in managing a new category, key to vehicle performance, that is a notable cost driver and subject to manufacturing shortages.
In particular, the global semiconductor shortages we experienced between 2020-2022 impacted almost every sector. Whilst the disruption for the automotive sector is largely viewed to be over5, it is worth considering the power electronics sector specifically. Major Silicone Carbide semiconductor manufacturers, and their capabilities and capacity must be firmly grasped. Currently, over 90% of the global manufacturing capacity is divided between biggest 5 suppliers (ST Electronics , onsemi, Infineon, Wolfspeed and ROHM)6 and vehicle manufacturers are being faced with key challenges:
• How to ensure competitive edge in design and performance?
• How to secure capacity and continuity of supply?
• How to protect IP ?
2
EV Inverter: Changing vehicle manufacturers strategies and key trends
Vehicle manufacturers have recognised that with growing EV volumes came the importance of developing their EV powertrain strategies that would embed resilient supply chains in the backdrop of a fragile market. With a more creative procurement and engineering approach to fully unlock potential cost and technological advancement opportunities.
The diagram below shows few simplified scenarios of cooperation between semiconductor manufacturers, inverter manufacturers and vehicle manufacturers.
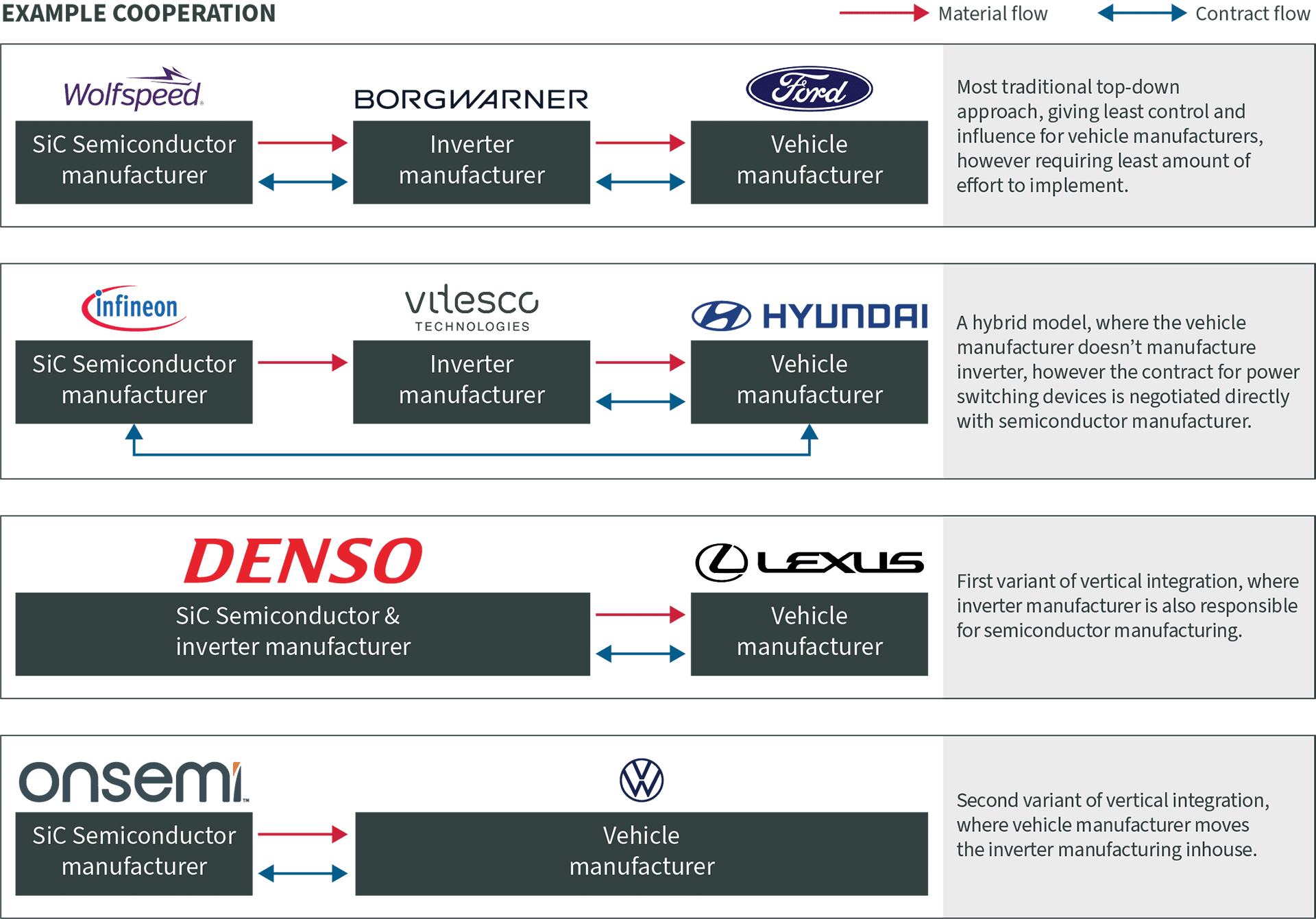
In the last few years, we have observed the materialisation of a new sub-sector and with it, several emerging trends:
Direct semiconductor manufacturers & vehicle manufacturers partnerships
The industry identified opportunities early on to enter into synergetic partnerships, on one-hand to leverage the market breadth and volume of mass-market Automotive OEMs, and in return, increase the competitiveness through first-to-market rights for new generations of SiC modules / switches. As such many of the semiconductor and vehicle manufacturers entered into partnerships such as, Infineon & Hyundai, Onsemi & Tesla, Infineon & Stellantis, and Wolfspeed & Mercedes-Benz, amongst others.
Some of the other key benefits of this approach was direct price negotiation & capacity booking, allowing vehicle manufacturers to regain purchasing power when contracting with inverter manufacturers. Semiconductor manufacturers benefited via multi-year supply agreements and related procurement commitments, allowing them to de-risk further investments in the R&D and manufacturing capabilities.
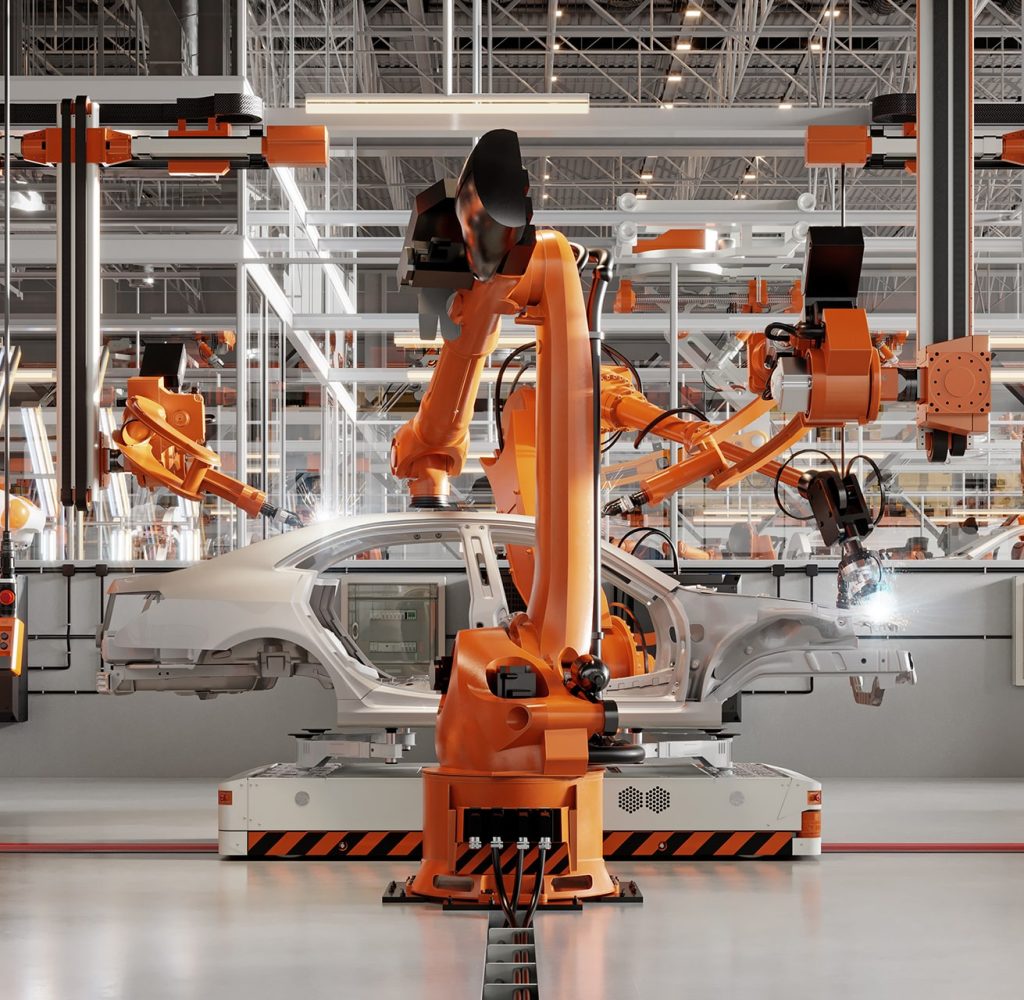
Vertical integration
One of the natural next steps in electric powertrain supply chain design was increased vertical integration. Vehicle manufacturers realised the urgency of the ICE to EV transition and related challenges. In-house development and manufacturing bring several benefits:
A. Increased control over the product, both in terms of design as well as cost
B. No need to compromise with inverter manufacturer requirements
C. Ability to reduce logistic costs & integrate with existing supply chain
D. Possibility to utilise labour resources that would be otherwise dedicated to ICE engines manufacturing.
Initial challenges in this approach were capability shortages and the upfront capital investment required to get the rate of return and the volume throughput. One of the early adopters of this model was Tesla and for many years they remained the only vehicle manufacturer who designed and manufactured inverters in-house.
As the industry has moved forward, with increasing environmental policies creating waves towards use and applications of greener technologies, we see other automotive OEMs following suit (i.e., VW group); who have recognised the technical and engineering opportunities to improve systems integration and better life-cycle management by bringing technology in-house, redeploying and retraining existing capability within their organisation, as well as establish a longer-term cost-conscious advantage, particularly given the significance of other cost drivers in EVs, such as batteries.
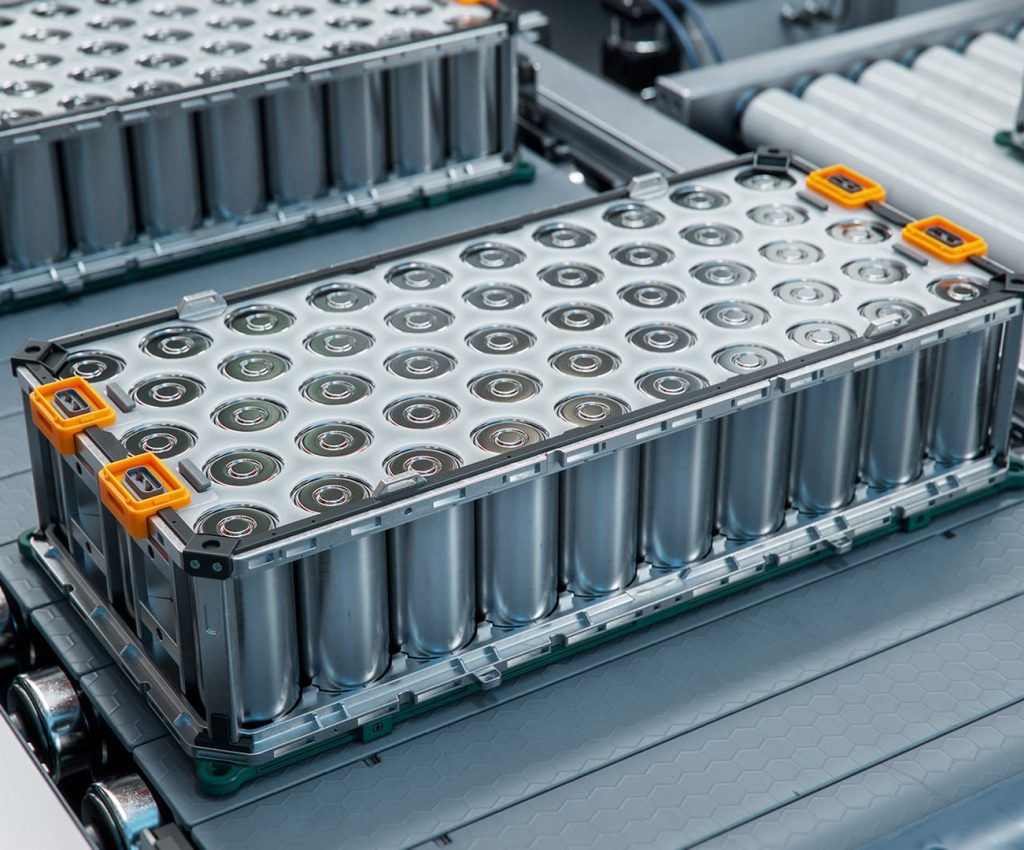
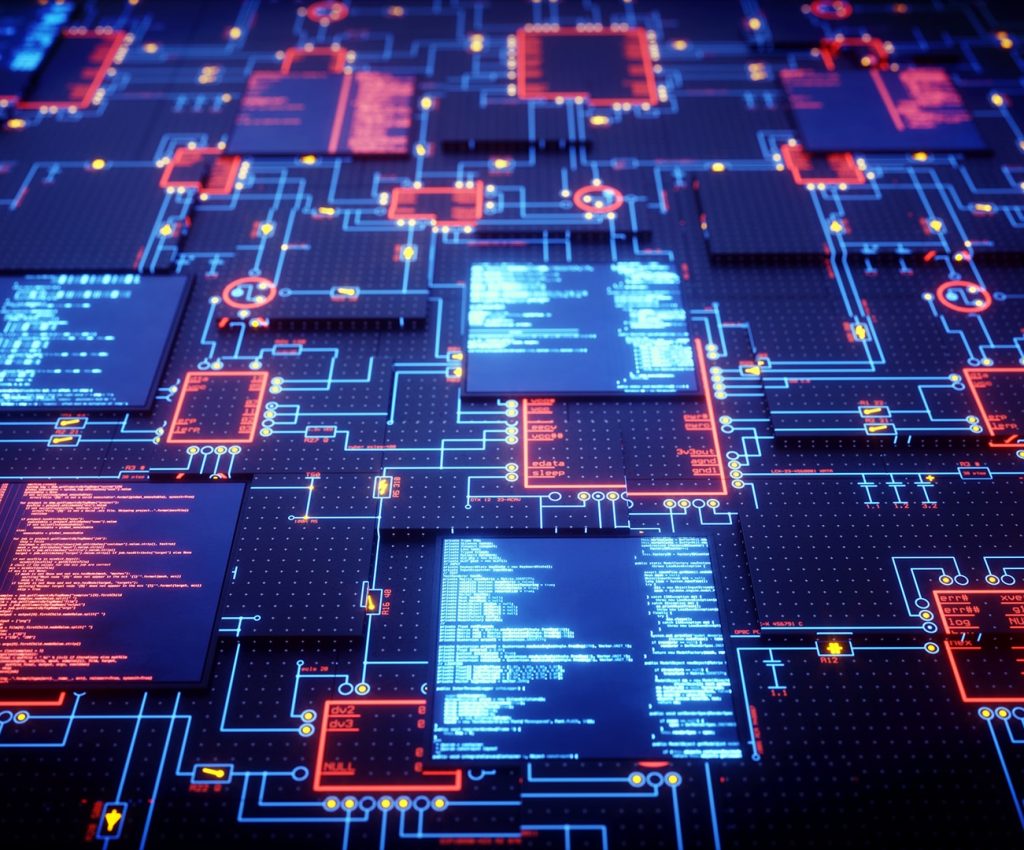
Modular design
The key design advantage driving in-house inverter development and manufacturing is the ability to design an inverter employing a modular approach. Tesla was the first manufacturer to implement this strategy, with all vehicle models using the same inverter . The differentiator between models has ultimately been power output – driven by two variables: (1.) the number of discrete switches soldered onto a board and (2) software configuration.
Despite higher initial investment and design complexity, this approach has allowed Tesla to significantly increase the annual volume of all of the other components (i.e., busbars, housings, PCBAs) and as a result, reduce cost through economies of scale.
This trend is now being adopted by all major vehicle manufacturers as it fits seamlessly with their well-established vehicle platform design approach.
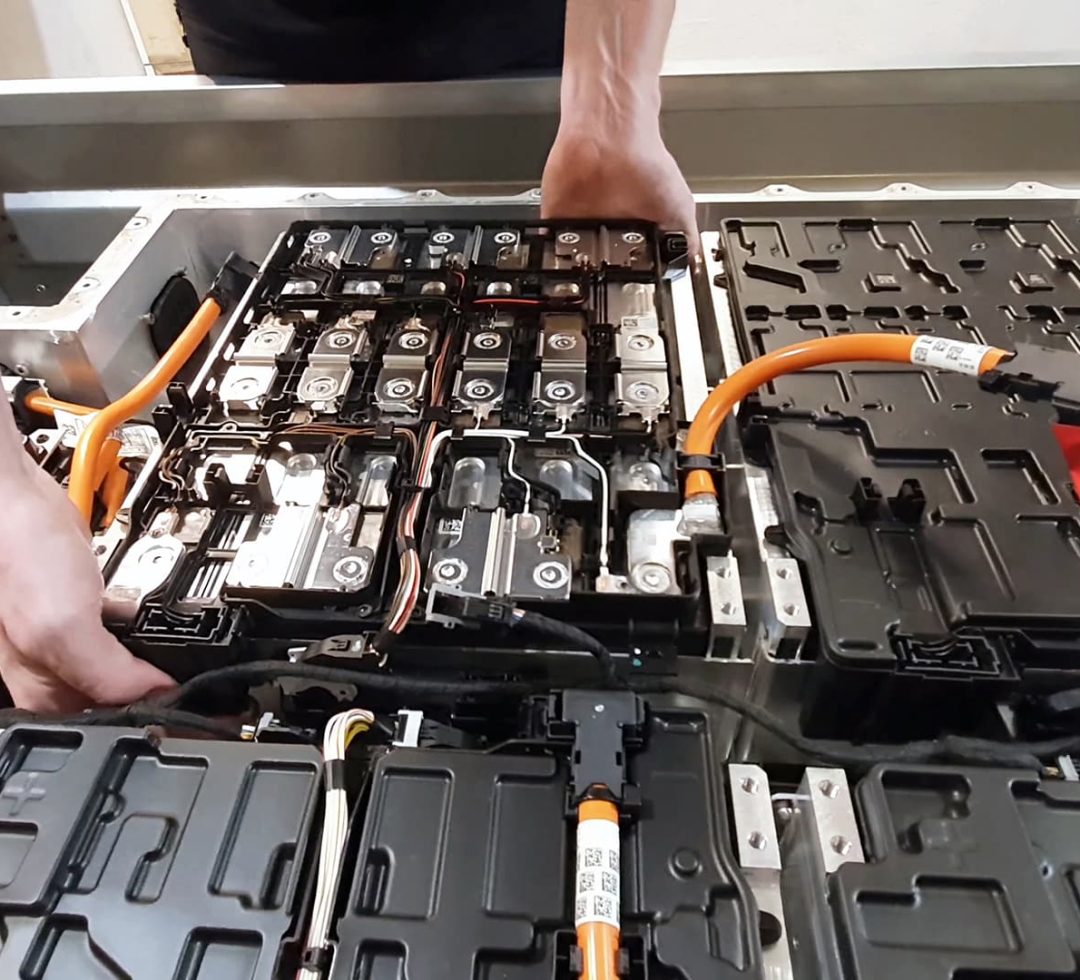
Integrated Drive Units
Integrated Drive Units (sometimes called an e-axle) is yet another step in the direction of unification, standardisation and cost reduction. Whilst the traditional approach utilised separate e-motors and inverters connected via busbars and/or cables, an increasing number of manufacturers are now unveiling their highly integrated designs, with the ambition of creating one assembly with all the required drivetrain elements, such as e-motor, inverter, transmission, driveshaft, differential and axles.
This approach has several advantages over the standard assembly: higher efficiency / lower energy losses, increased lifespan, lower noise, better packaging, reduced space and weight requirements.
Combined with modular design, this creates a great opportunity to complement the platform vehicle approach and maximise economies of scale benefits.
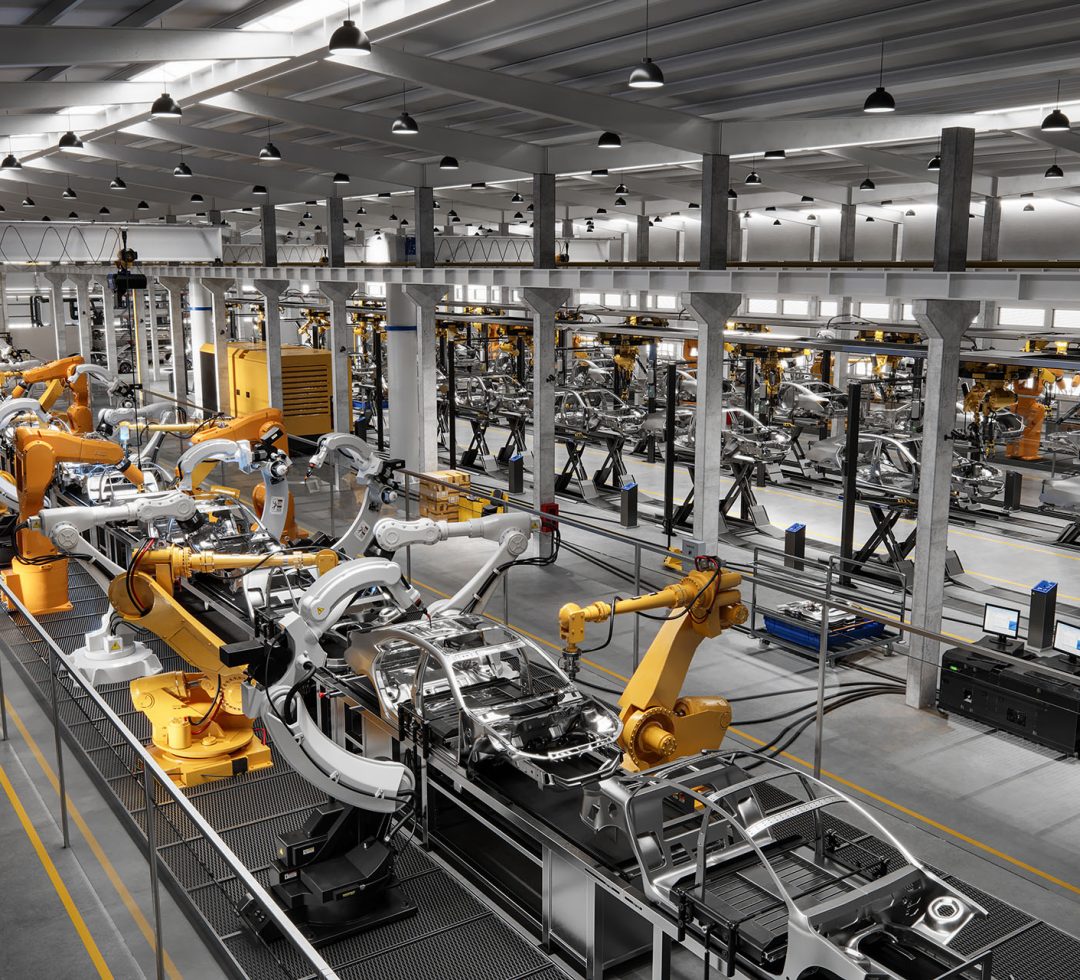
3
EV Inverter: Shift in market power
Initial widespread adoption of SiC modules led to global shortages of SiC wafer supply in 2021 and 2022. As a result, vehicle manufacturers began to reserve capacity through multi-year agreements. Large demand and relatively secure position of semiconductor manufacturers led to intensified efforts to increase the capacity. It is estimated that in 2023-2024 the investment in worldwide SiC fabrication & manufacturing plants reached over ~£17b7 8.
With new plants being commissioned, the problem of lack of supply is no longer an immediate risk. At the same time, constant development efforts improved the products performance across the board, meaning that the differences between various products are minimal.
As a result, semiconductor manufacturers have had to investigate new options to ensure healthy market share. It is important to note that not all semiconductor manufacturers have the capabilities to manufacture SiC wafers in-house. For example, Infineon currently uses SiC wafers supplied by Wolfspeed9 and targets power module manufacturing as the key offering.
Other competitors, such as onsemi, ROHM or STMicroelectronics are all investing in developing internal capabilities, however to date they still partially rely on external wafer supply.
An additional challenge presented to current market leaders are new entrants and in particular, the rapid development of technological capability coming from China. Bosch has already begun work on developing in-house SiC wafer manufacturing, planning to invest $1.5b in the new facility. Chinese players such as SICC, TankeBlue or San’an have all increased their capacity to levels allowing them to supply more than half of the current global demand and their partnerships and joint ventures with companies such as Bosch, Infineon or STMicroelectronics poses a sizeable threat to current market leaders10.
Existing challenges and the dynamic nature of the wafer and semiconductor manufacturing sector means that vehicle manufacturers are gaining more and more control of the narrative. The abundance of choice, growing volume and technological advancements are expected to create an environment in which cost competitiveness will become one of the key elements of success.
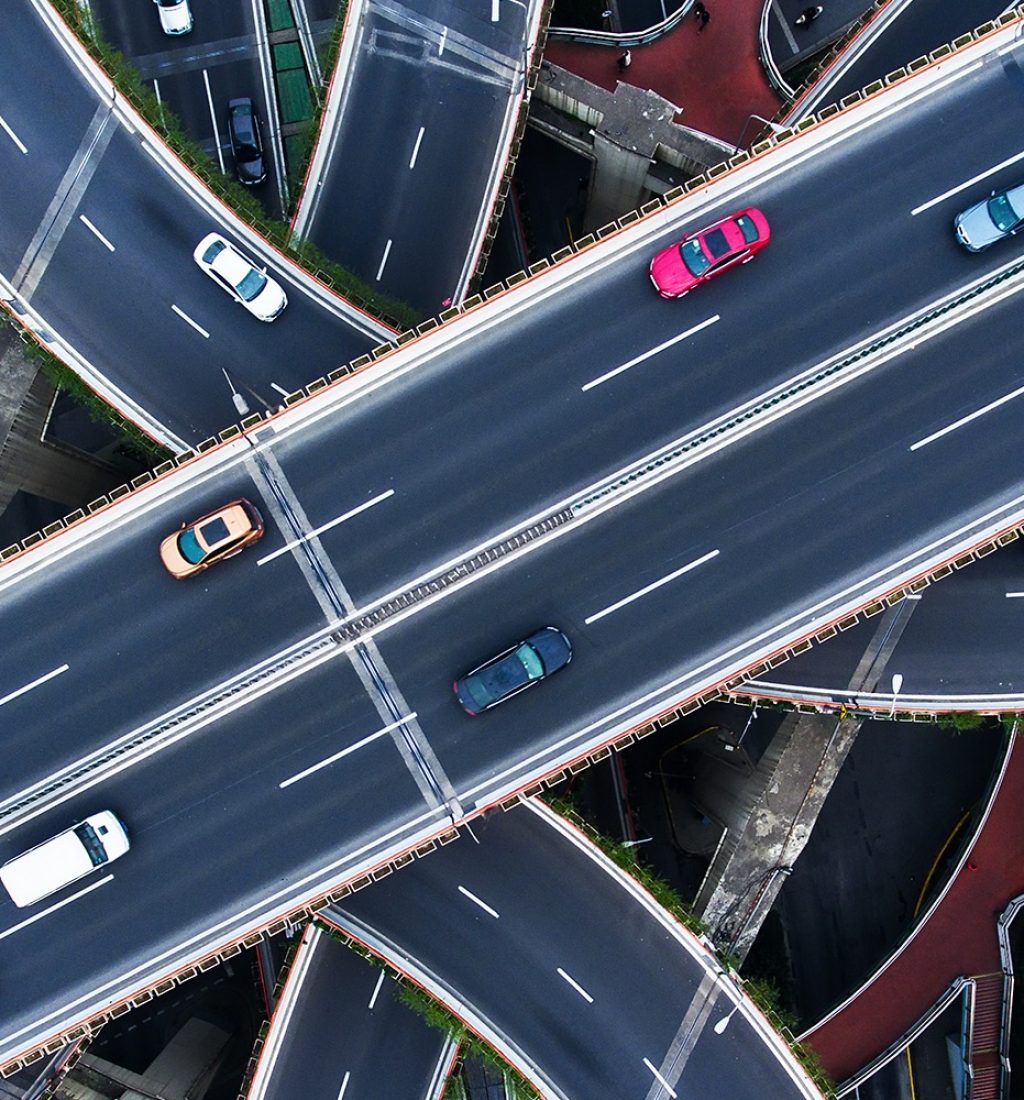
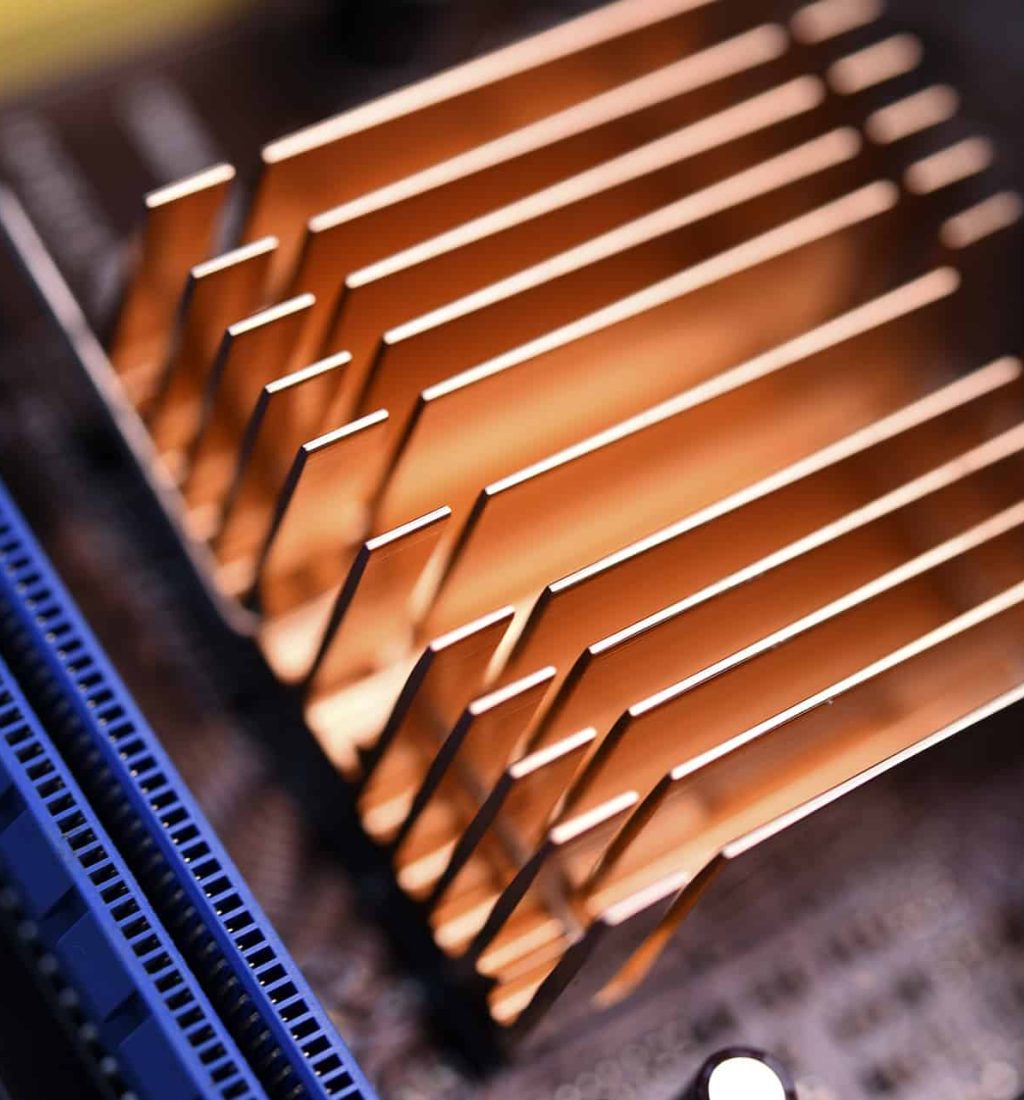
4
EV Inverter: Future outlook – building resilience and security of market share
Automotive market volatility
One of the key influencing factors in terms of inverter commodity strategy is simply the nature of the automotive EV market. From 2015-2020 we observed strong commitments from major vehicle manufacturers to go fully electric at pace, but we can now observe major brands delaying or cancelling some of their previous plans in favour of hybrid vehicles that enables them to utilise existing vehicle platforms. Examples include Porsche removing the target to be 80% electric by 203011, Mercedes cancelling the whole MB.EA platform12 or VW decelerating its ID brand introduction pace and scrapping EV factory plans13.
This is mainly a result of customer demand, which to much extent has been influenced by geopolitical and economic changes – in 2024 alone, almost half of the world’s population experienced elections in their countries. This has influenced the expediency towards electrification and decarbonation as a consequence of changes in government incentives, schemes, affordability and on-going running costs.
These changes have forced semiconductor manufacturers to recalibrate production capacity, forcing them to re-evaluate their development roadmaps. All of this has a considerable impact on the long-term agreements, especially in cases where volume-based commitments have been made. Suppliers as well as the buyers will need to apply creative procurement solutions to carefully tailor the contracts and agreements and find the right balance between ensuring the continuity of supply, right level of flexibility and fair compensation clauses.
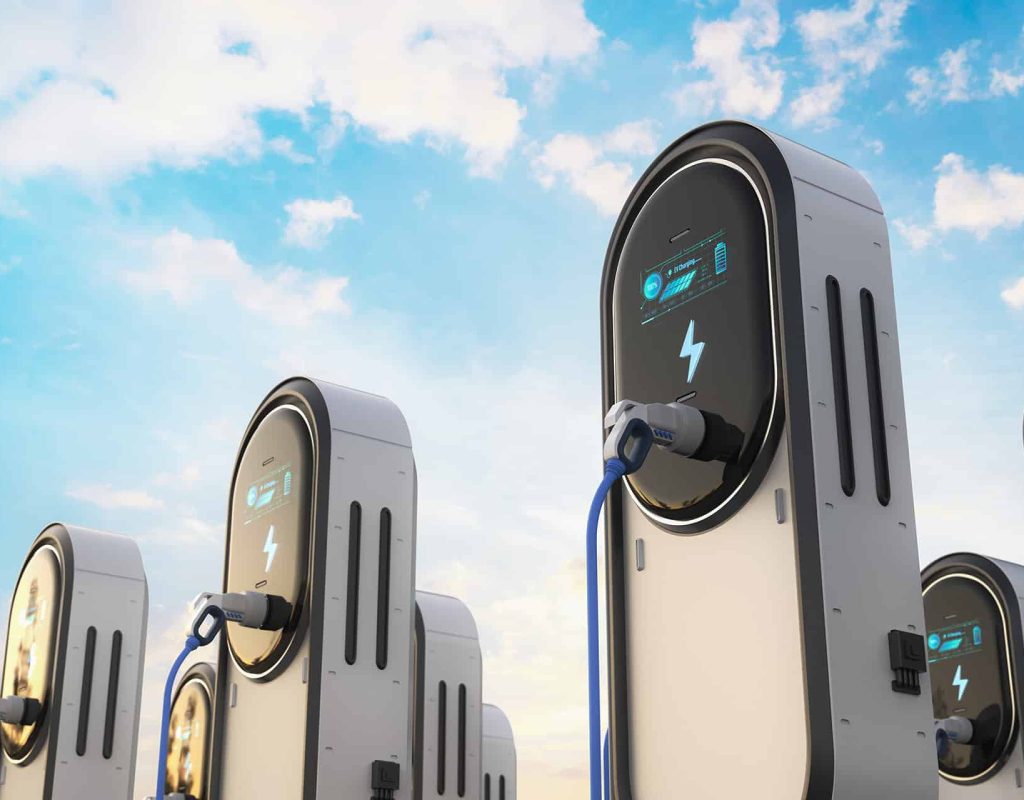
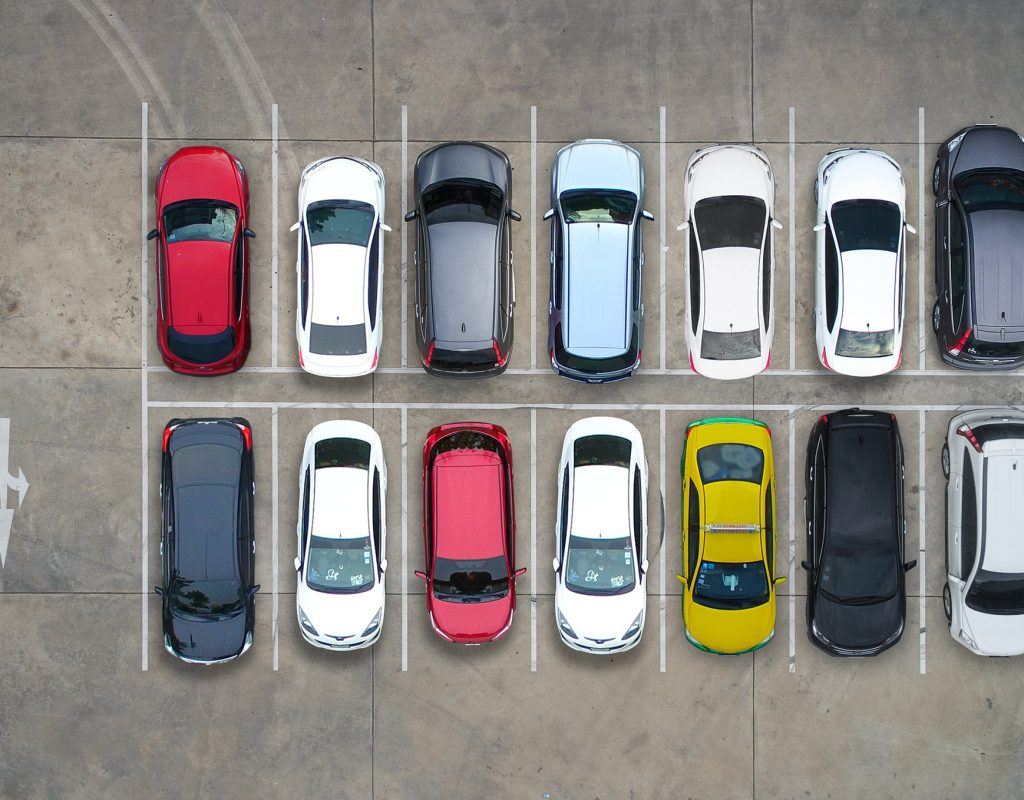
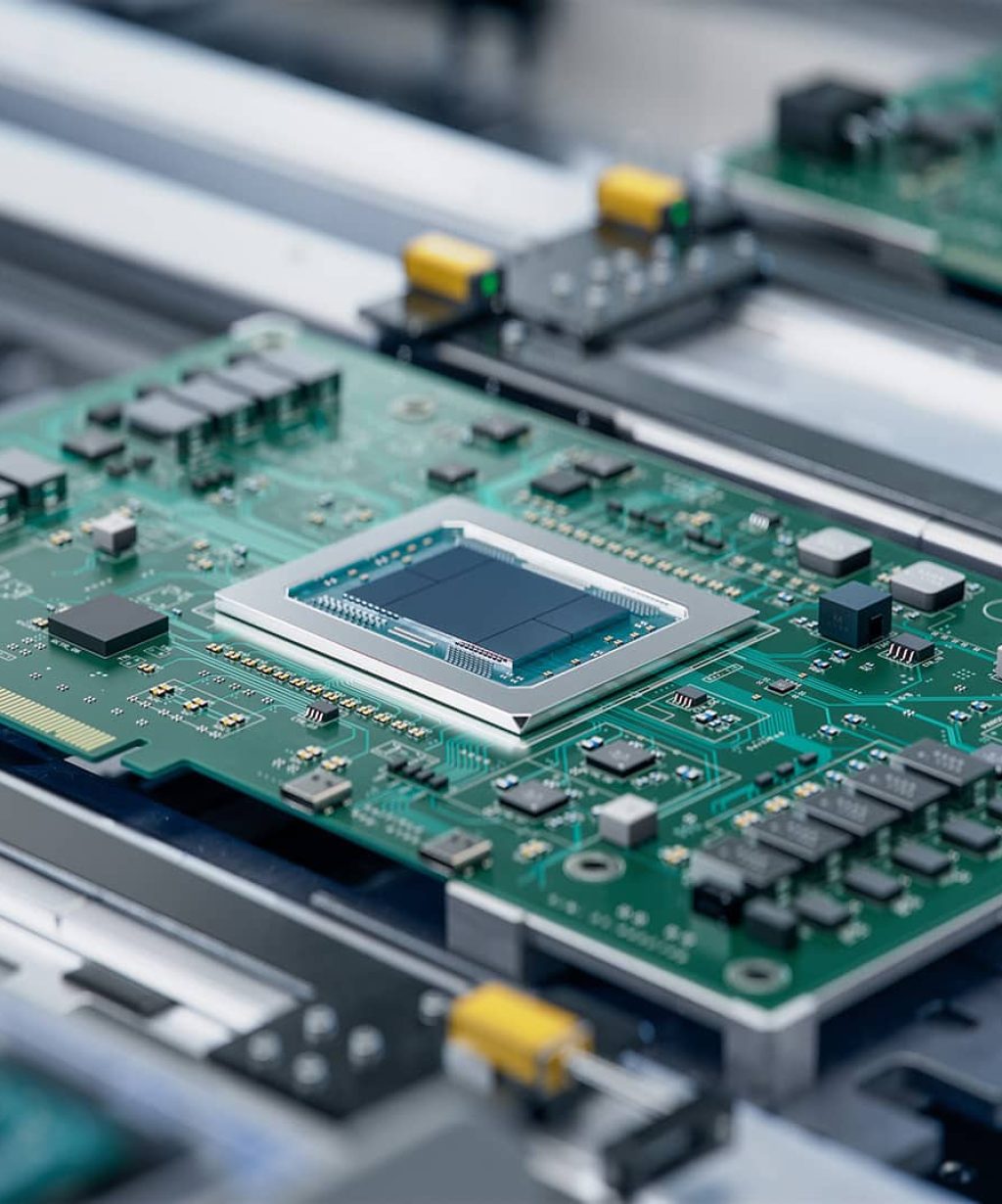
Technology
With the latest designs utilising SiC power switches, automotive inverters can consistently reach the peak efficiency of over 99%14 15. Latest 800V architecture designs dropped the charging times to ~20 minutes (depending on capacity and charger power)16. Achieving those parameters means that no major design changes are expected in the inverter space, instead, we should be looking forward to a series of evolutionary steps.
To remain competitive, it is essential to ensure that the inverters and powertrains are optimised not only for best performance and simplicity, but also for lowest cost. In the next few years we should expect to see more DfX and VA/VE activities take place to iteratively improve the design.
Some of the key design trends we might observe in the future include:
Vertical integration – i.e., reducing overall complexity of the powertrain by integrating key elements including inverter in one assembly
Modular design, allowing to more easily adapt to market demand, without the need for costly re-development (i.e., through modulating power of the inverter by using variants of power switches & software programming rather than using completely different inverter).
Cost & Supply Chain
Last but not least, with the changing outlook on the capacity shortages and purchasing power, the design of the Supply Chain and related cost should be re-evaluated. Modular design will unlock further economies of scale and new make vs buy opportunities. New manufacturing plants will increase semiconductor market competitiveness. Impact of tariffs and raw material cost changes will influence existing business cases.
This changing landscape means that now more than ever, it’s important for the vehicle manufacturers to fully understand what they are paying for and how to ensure their approach is the most cost effective. One of the established mechanisms that will allow manufacturers to gain that knowledge is should-costing principles, a well-known cost engineering approach that has proven its value time and time again. Vehicle manufacturers will now have to ensure they have the right capabilities to fully understand the electronics components sector and be able to verify the cost and support their Supply Chain on a journey of improving efficiency.
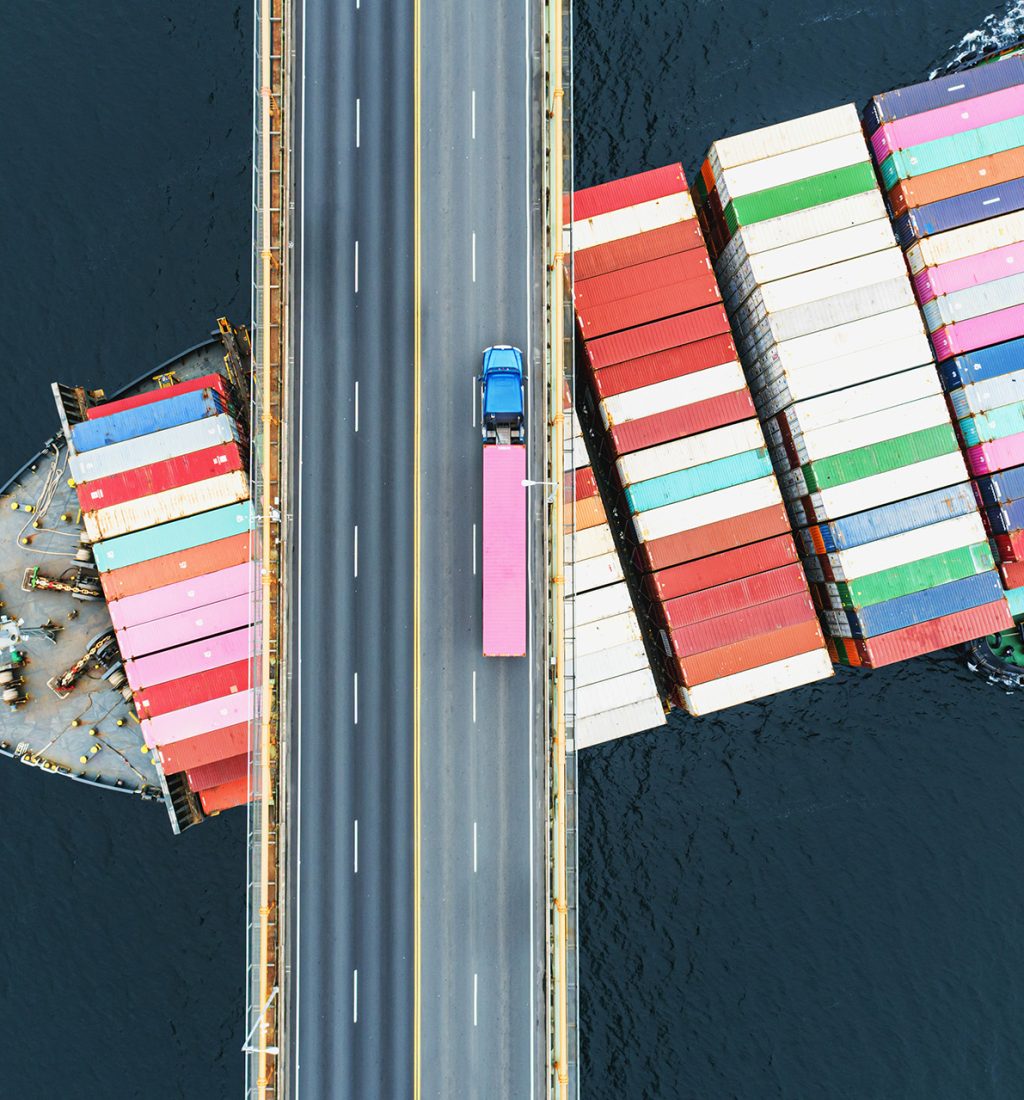
5
Conclusion
The Power Electronics area is a great example of how emerging technologies and the changing electronic components market indirectly impacts the end customer. Future outlook for EV inverters involves several key factors. Market volatility is a significant concern, with major automotive manufacturers adjusting their EV plans due to fluctuating customer demand. This shift has reduced capacity issues, giving buyers more leverage and prompting semiconductor manufacturers to reassess their strategies. Technologically, SiC power switches have already enabled automotive inverters to achieve over 99% efficiency and reduce charging times to around 20 minutes.
Therefore, future improvements will focus on overall design and cost optimisation through design for excellence (DfX) and value analysis/value engineering (VA/VE) activities. Trends such as vertical integration and modular design will help reduce powertrain complexity and adapt to market demands without costly redevelopment. In order to fully unlock economies of scale, manufacturers must thoroughly understand costs and use should cost models to ensure cost-effective approaches and support supply chain efficiency improvements. This comprehensive understanding will be crucial for staying competitive in the dynamic EV market.
With the shared global goal of sustainable future, technology will become an intrinsic part of not only automotive, but many other sectors. As such, over the next few years, we will observe many sector crossovers, and it will become even more important for a variety of manufacturers to increase their understanding and ownership of electronic components commodity.
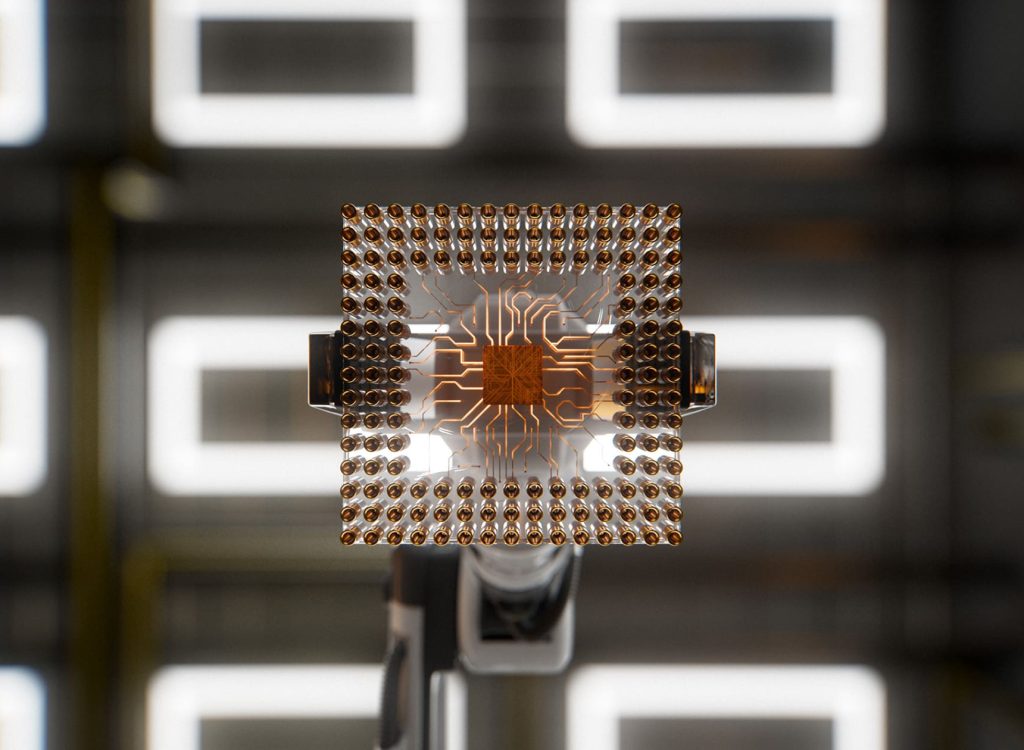
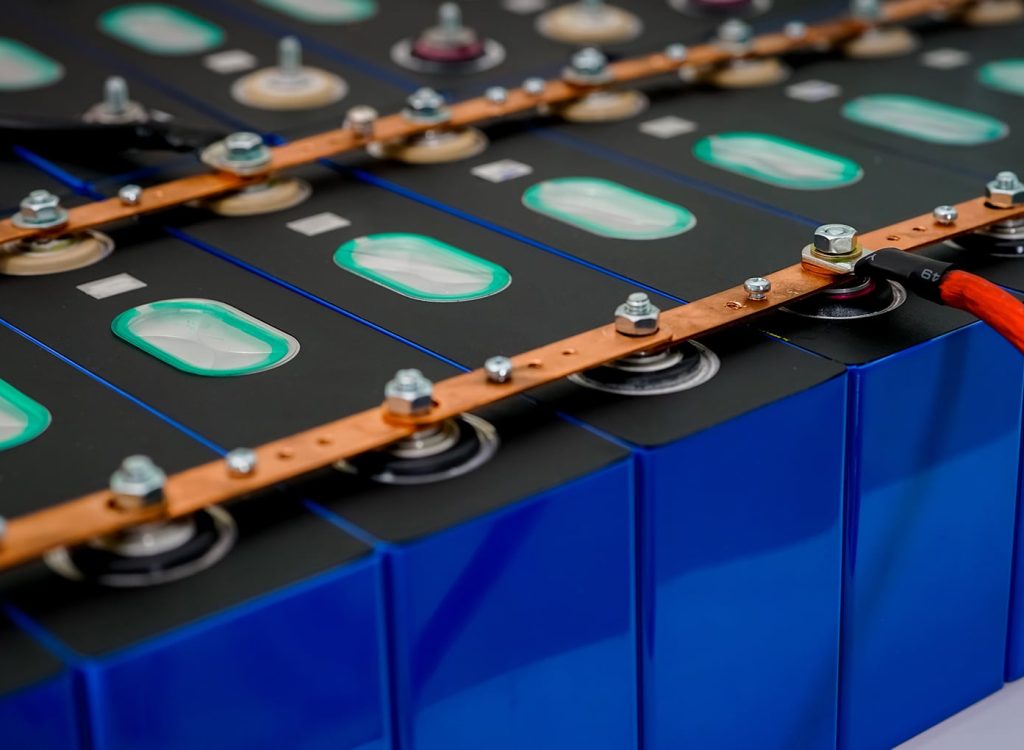
Authors
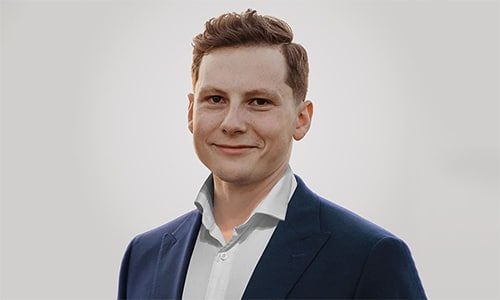
Artur Ziewalicz
Principal Consultant
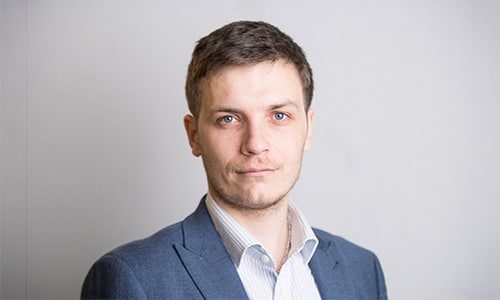
Oskars Veberis
Principal Consultant
Sources
1. “Automotive electronics cost as a percentage of total car cost worldwide from 1970 to 2030,” [Online]. Available: https://www.statista.com/statistics/277931/automotive-electronics-cost-as-a-share-of-total-car-cost-worldwide/.
2. “Bosch’s revenue in FY 2023, by segment,” [Online]. Available: https://www.statista.com/statistics/271675/bosch-revenue-by-segment/#:~:text=In%20the%202023%20fiscal%20year,euros%20in%20revenue%20for%20Bosch..
3. “Global automotive inverter market size in 2020, by region or country,” [Online]. Available: https://www.statista.com/statistics/1372633/global-automotive-inverter-market-by-region-or-country/.
4. “Automotive and Transportation – Automotive Power Electronics Market,” [Online]. Available: https://www.reportsanddata.com/report-detail/automotive-power-electronics-market.
5. “The semiconductor shortage is – mostly – over for the auto industry,” [Online]. Available: https://www.spglobal.com/mobility/en/research-analysis/the-semiconductor-shortage-is-mostly-over-for-the-auto-industry.html.
6. “2023 Global Market Share – Sic Power Devices,” [Online]. Available: https://www.semiconductor-today.com/news_items/2024/jun/trendforce-200624.shtml.
7. “The world’s biggest SiC fab,” [Online]. Available: https://compoundsemiconductor.net/article/118342/The_world%E2%80%99s_biggest_SiC_fab.
8. “Silicon carbide: from gold rush to commodity?,” [Online]. Available: https://www.yolegroup.com/strategy-insights/silicon-carbide-from-gold-rush-to-commodity/.
9. “Infineon and Wolfspeed extend their 150mm SiC wafer supply agreement over multiple years,” [Online]. Available: https://www.powerelectronicsnews.com/infineon-and-wolfspeed-extend-their-150mm-sic-wafer-supply-agreement-over-multiple-years/#:~:text=Infineon%20Technologies%20is%20implementing%20a,chain%20for%20the%20foreseeable%20future.
10. “More than half of the world’s SiC wafers might come from China in 2024,” [Online]. Available: https://www.digitimes.com/news/a20231023PD210/silicon-carbide-china-compound-semiconductor-ic-manufacturing-sic.html.
11.“Porsche ditches electric car targets as demand fails to accelerate,” [Online]. Available: https://www.euronews.com/business/2024/07/24/porsche-lets-go-of-electric-car-targets-as-demand-fails-to-accelerate#:~:text=Luxury%20car%20maker%20Porsche%20has,new%20sales%20targets%20by%202030..
12. “Mercedes has reportedly cancelled an entire EV platform,” [Online]. Available: https://www.topgear.com/car-news/electric/mercedes-has-reportedly-cancelled-entire-ev-platform.
13. “Volkswagen Walks Back EV-or-Bust Strategy That Rankled Rivals,” [Online]. Available: https://www.bloomberg.com/news/articles/2024-05-16/volkswagen-walks-back-ev-or-bust-strategy-that-rankled-rivals?embedded-checkout=true.
14. “Automotive traction inverter hits efficiency 98.5% at 5% load (and peaks at 99.57%),” [Online]. Available: https://www.electronicsweekly.com/news/design/automotive-traction-inverter-hits-efficiency-98-5-at-5-load-and-peaks-at-99-57-2023-03/#:~:text=21st%20March%202023-,Automotive%20traction%20inverter%20hits%20efficiency%2098.5%25%20at%205%25%20load%20(,Peak%2.
15. “McLaren Applied launches IPG5-x: a highly flexible and easy to integrate 800V SiC inverter,” [Online]. Available: https://www.automotivepurchasingandsupplychain.com/mclaren-applied-launches-ipg5-x-a-highly-flexible-and-easy-to-integrate-800v-sic-inverter/.
16. “THE CHARGING PROCESS,” [Online]. Available: https://media.porsche.com/mediakit/taycan/en/porsche-taycan/das-laden#:~:text=With%20the%20Performance%20Battery%2C%20the,5.5%20minutes%20under%20these%20conditions.
Explore Vendigital