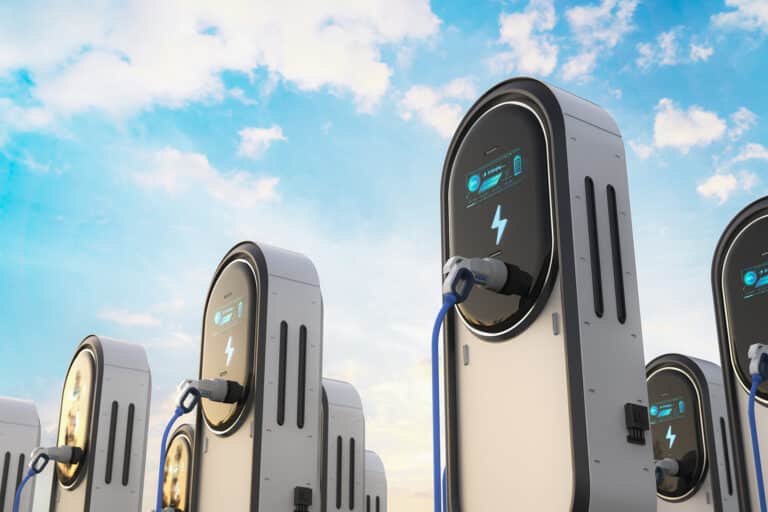
It’s time to embrace Chinese EV capability
EV makers in the UK and Europe are warning that Zero Emission Mandates are simply not doable and subdued levels of demand could force them to close factories. Should the industry embrace Chinese capability before it’s too late?