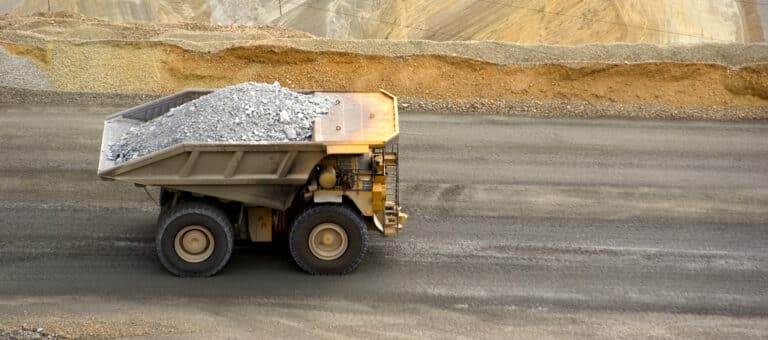
Increasing capacity and meeting decarbonisation goals – can it be done?
We discuss the cost and infrastructure considerations of switching to an all-electric fleet of off-highway vehicles.
Alan March is a principal cost and value engineer at Vendigital. He recently shared his insights with E&T.
Innovative approaches to cost modelling and supply-chain know-how are helping automotive manufacturers get ahead in the race to achieve net-zero emissions by 2050. But could the sector decarbonise its products and processes five years ahead of time?
Achieving net-zero emissions is a major challenge for process manufacturers across the board, but more so for those in the global automotive sector. This is largely due to their reliance on carbon-intensive processes and use of raw materials that may be difficult to extract or are only available in distant territories or regions of the world. Against the odds, however, some automotive manufacturers are succeeding in applying smart supply-chain thinking and advanced cost-modelling techniques to decarbonise their products and processes ahead of other industries.
Among the key drivers in the push to decarbonise products and processes is growing stakeholder interest in environmental, social and corporate governance (ESG) performance, which has led most global car makers and Tier One OEMs to strengthen reporting in this area. The speed of the switch to electric vehicles and increasing consumer awareness of the climate crisis is further emphasising the need to accelerate decarbonisation programmes.
Underlining the growing focus on ESG performance, research conducted by Vendigital with UK-based manufacturing businesses last year found that 80 per cent of board-level executives think it has a direct impact on customers’ buying decisions. However, about two-thirds (69 per cent) would only adopt a net-zero sourcing strategy if it delivered a net cost benefit too.
Early evidence of the rush to decarbonise across the automotive industry is the high level of investment in innovation activity to tackle key carbon drivers, such as lithium-ion batteries. In particular, battery manufacturers are searching for new chemistries that could help to reduce reliance on minerals such as lithium, cobalt and nickel. While a battery-powered engine has a lower carbon footprint than an internal combustion engine, hard-rock mining and extraction techniques, combined with transportation over long distances, carry a significant carbon footprint. Synthesising the raw materials used to produce lithium-ion batteries also involves heating them to between 800°C and 1,000°C, which can only be achieved cost effectively by burning fossil fuels, further adding to their carbon footprint.
In automotive production, the energy-intensive processes used to make steel, aluminium, plastics, glass and rubber are other major contributors to the whole-life carbon footprint of an EV. Innovating to find ways to improve process efficiency, minimise waste and reuse materials after the vehicle has reached the end of its life is an accelerating trend, particularly as early EVs are now approaching the end of their ten-year lifespan. Battery manufacturers are already recycling materials used in the production of lithium-ion batteries, and the hope is that, in time, this activity will reduce reliance on virgin supplies of diminishing earth minerals.
Key to understanding the whole-life carbon footprint of each process or product is accurate data, of course – data about where emissions are being generated and the scale on which they are being released into the environment. This can then be used to guide green investment decisions. For example, a 15-year-old furnace used in the manufacture of forgings is likely to be much less efficient than a modern, state-of-the-art design. This will use a lot less energy, get to temperature faster and hold its heat for longer. As a result, it could achieve more output in a shorter time, reducing the carbon footprint of each manufactured component significantly in some cases. This shows how micro-level understanding of where carbon emissions are coming from and how much are being generated can be used to inform investment decisions and reduce the end product’s whole-life carbon footprint.
Some vehicle manufacturers and Tier One suppliers are already ahead of the game when it comes to understanding the end-to-end carbon footprint of their supply chain and taking steps to reduce it. The current focus on nearshoring and other smart supply-chain thinking is helping to protect sources of supply at the same time as slashing transportation costs and decarbonising processes. Most start by identifying the top ten carbon contributors and plot this information against cost and margin considerations. Data-based insights can then help to guide decisions about whether to continue to do things the same way or to make changes by switching to a different supplier, using alternative products or materials or investing in more efficient machinery.
When using data to inform process or product changes of any type, it is important that businesses adhere to recognised industry standards. Data input should be subjected to a robust critical analysis to test its accuracy and reliability. Once the systems used to gather and process the incoming data have been certified against ISO 14064 standard, they can be relied upon to guide investment decisions.
Understanding the principles of cost modelling can enable businesses across sectors to decarbonise their products and processes and manage their cost base at the same time. If decision makers know the ‘cost’ and ‘carbon’ drivers within their business, they can take action to change things or invest to make them better. Most business leaders appreciate how challenging it can be to pinpoint exactly the right time to reinvest in new machinery, over the benefit of using legacy process equipment, but cost modelling can make such decisions much easier.
The automotive industry is leading the way to net-zero emissions for a number of reasons. The sheer volume of new vehicles produced globally each year and the complex nature of global supply chains make it all the more important to take action early. The pace of the shift to EVs, mostly driven by fiscal incentives and the rising cost of fuel, is also creating an opportunity to make changes that will speed up decarbonisation programmes and streamline costs at the same time.
Can the automotive industry achieve net zero by 2045? Probably sooner if it uses data as its guide.
Sign up to get the latest insights from Vendigital
Get in touch
Related Insights
We discuss the cost and infrastructure considerations of switching to an all-electric fleet of off-highway vehicles.
EV makers in the UK and Europe are warning that Zero Emission Mandates are simply not doable and subdued levels of demand could force them to close factories. Should the industry embrace Chinese capability before it’s too late?
In our latest report we examine the impact of power electronics and the importance of inverters in EV manufacturing.
Subscribe to our newsletter